Regenerative Thermal Oxidizer
RTO Thermal Oxidizer /Regenerative Thermal Oxidizer System
One of the most widely accepted air pollution control technologies across the industry today is the regenerative thermal oxidizer system, commonly known as RTO. RTO uses a ceramic bed heated from the previous oxidation cycle to preheat the input gases to partially oxidize them. The preheated gas enters the combustion chamber, which is heated by an external fuel source to reach the target oxidation temperature between 760°C (1,400 °F) and 820°C (1,510 °F). For applications requiring maximum damage, the final temperature may be as high as 1,100 °C (2,010 °F). Air flow ranges from 2.4 to 240 standard cubic meters per second.
RTO (regenerative thermal oxidizer) is versatile and highly efficient – up to 95% thermal efficiency. They are often used to reduce solvents, fumes, odors, etc. from all walks of life. RTO regenerative thermal oxidizers are ideal for low to high VOC concentration ranges up to 10 g/m3 solvents. There are many types of regenerative thermal oxidizers on the market today that have a volatile organic compound (VOC) oxidation or destruction efficiency of 99.5+%. The ceramic heat exchanger in the tower can be designed for thermal efficiency of up to 97+%.
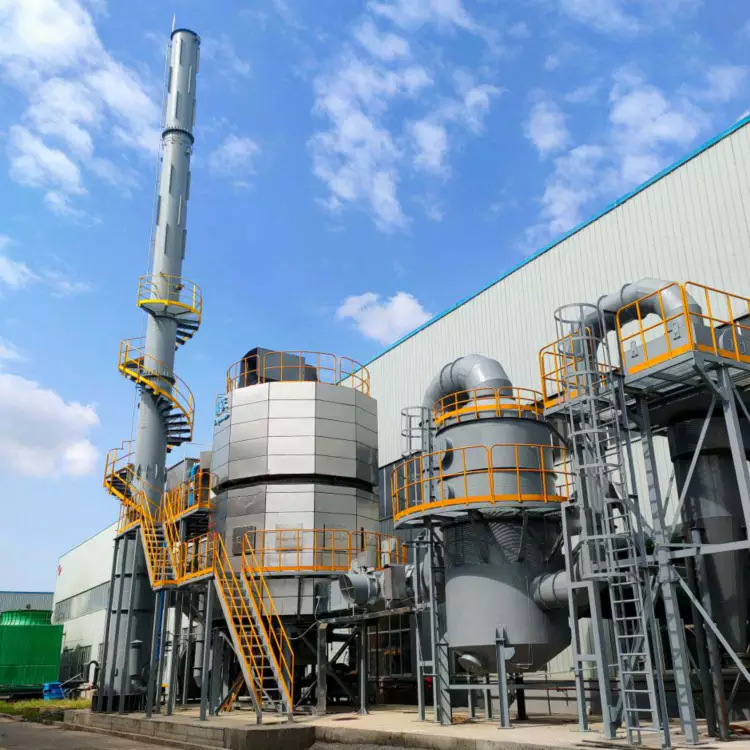
Rotary RTO Regenerative Thermal Oxidizer
Toptank rotary RTO high-end products have reached the world’s advanced level of product technology, with high-end quality to the market users more high-end choice, to help more enterprises to successfully embark on the road to green development, to achieve economic development and environmental protection win-win situation.
Rotary Regenerative Thermal Oxidizer Features
- Top quality stability: top purchased parts configuration, selection of super wear-resistant anti-aging fluoro silicone sealing materials;
- Excellent insulation and energy saving: vacuum shell insulation structure, reduce convection heat dissipation, energy saving effect increased by 3%;
- Super operation safety: top safety components, safety control software with artificial intelligence learning judgment and failure prediction ability;
- Convenient network interaction: mobile APP real-time online cloud monitoring, friendly network data interaction function;
- Aesthetic design of The Times: future industrial appearance, advanced anti-corrosion and anti-rust surface treatment process.
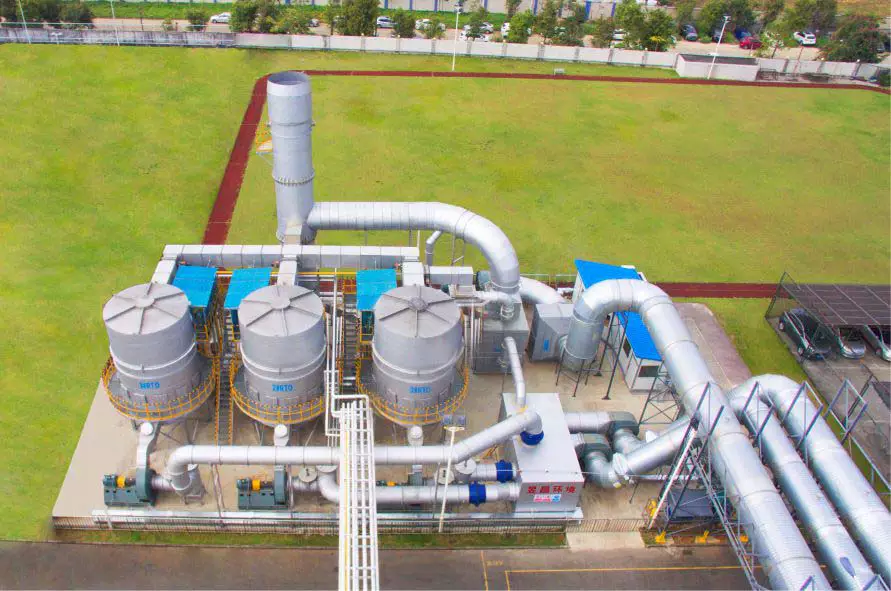
RTO systems destroy volatile organic compounds in industrial waste gases to reduce air pollution.
What is a Regenerative Thermal Oxidizer?
A regenerative thermal oxide (RTO) is a combustion device that controls volatile organic compounds (VOCs), hazardous air pollutants (HAPs), and odors by converting emissions into (destructive) emissions and by using heat to convert emissions into CO2 and H2O and then release them into the atmosphere. RTO can achieve a thermal efficiency of up to 97% and destruction efficiency of over 99%.
RTO oxidant is considered one of the most advanced thermal oxidation systems in the world. Compared to other thermal oxidizers, regenerative thermal oxidizers (RTOS) have a thermal efficiency of up to 97%, and destruction efficiency may exceed 99%, which will give you the highest removal rate at the lowest life cycle cost. — Matched with industry-leading structures and design features, all deliver superior performance, significantly lower operating costs, and industry-leading reliability.
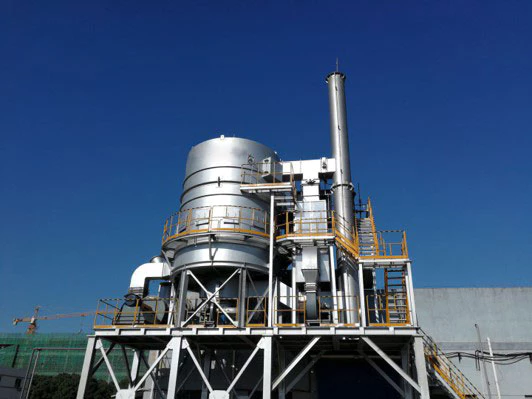
How Does a Regenerative Thermal Oxidizer Work?
- Regenerative thermal oxidizers (RTOS) work by pushing air filled with pollutants through the peroxide. usually with a system fan.
- The flow of air through the RTO is controlled by a valve that directs airflow into one of two heat exchangers (a chamber containing a ceramic dielectric bed).
- The RTO shall have at least two ceramic dielectric beds (saddles and/or structured dielectric blocks) as heat exchangers. As dirty air passes through the first medium bed, it absorbs heat from the hot ceramic medium and then enters the combustion chamber.
- In the combustion chamber, dirty air is kept at a temperature (> 1500°F) specific residence time (> 5 seconds). This oxidizes VOCs and HAP into carbon dioxide and water vapor.
- Hot and clean air leaves the combustion chamber and enters the second ceramic medium bed to absorb heat for reuse.
- The cooled clean air is then discharged into the atmosphere.
The valve changes direction every few minutes, thus reversing the direction of flow, so that heat transfer alternates between the two ceramic media beds. This is why RTO (regenerative thermal oxidizers) have high fuel efficiency and low operating costs, making them an ideal VOC reduction system.
RTO Regenerative Thermal Oxidizer Working Principle
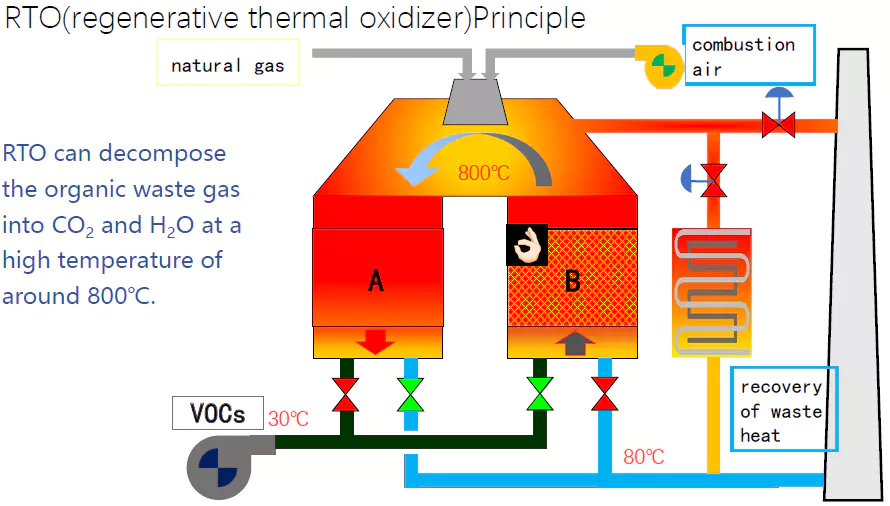
Regenerative thermal oxidizer process flow diagram
Rotary RTO Regenerative Thermal Oxidizers Design
12 heat storage packed beds are distributed in a circle and work alternately, with 5 in let and 5 out let, 1 purging, and 1 isolation
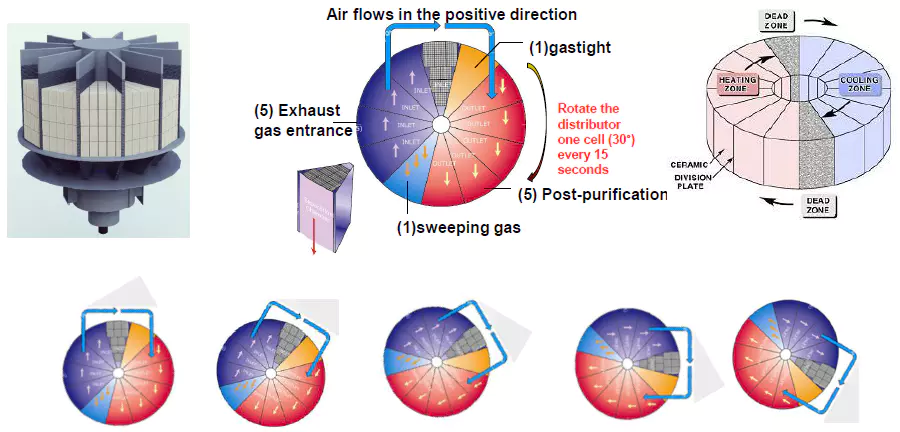
Regenerative thermal oxidizer diagram
Types of RTO
Performance comparison table of different types of RTO | ||||
Type | 2-Beds RTO | 3-Beds RTO | Rotary RTO | Remark |
Technology of iteration | First generation | Second generation | Third generation | |
Number of regenerators | 2 | 3 | 12 | |
Purification efficiency | 95% | 99% | 99.5% | |
Thermal efficiency | 90% | 95% | 97.0% | Temperature difference between inlet and outlet≤30℃ |
Occupation of land | 100% | 130% | 65% | Take 2-Beds RTO as the benchmark |
Technical Iterations of the RTO
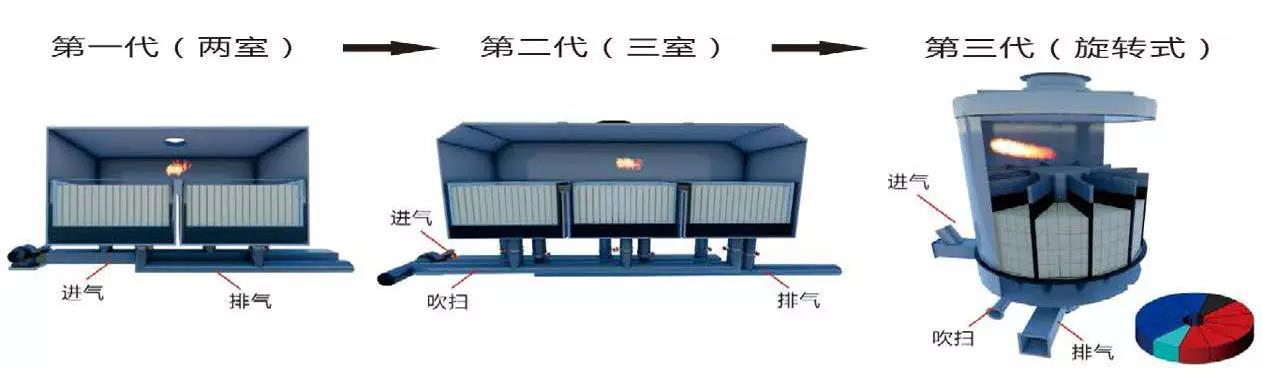
First generation(2-beds)
Temperature 120℃
Medium energy consumption
Purification efficiency 95%
Environmental protection does not meet the standard, thus eliminated
Second generation(3-beds)
Temperature 100℃
Medium energy consumption
Purification efficiency 99%
Meet environmental protection standard
Third generation(rotary RTO)
Temperature 60℃
Low energy consumption
Purification efficiency 99.5%
Meet environmental protection standard
The Structure of Rotary RTO
Rotary RTO comprises a combustion chamber, regenerative chamber, and rotary valve.
The furnace body is divided into 12 chambers, 5 inlet chambers, 5 outlet chambers, 1 cleaning chamber, and one isolation chamber.
The rotary valve is driven by the motor for continuous and uniform rotation. Under the rotary valve, the exhaust gas slowly switches continuously between 12 chambers. Its basic structure is shown in the figure on the right.
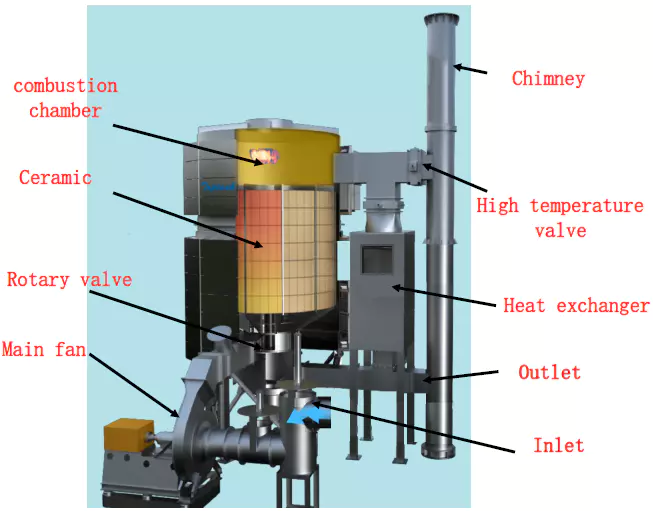

Generally speaking, the more regenerative chambers, the higher the purification and thermal efficiency. With the development of technology, the third generation OF RTO, namely rotary RTO, was born.
It has 12 circular regenerators and has the advantages of compact structure, small heat dissipation area, low energy consumption, high thermal efficiency, its purification efficiency can be up to 99.5%.
The Advantages of Rotary RTO
Ultra high purification efficiency 99.7%
Ultra high heat storage efficiency 97%
Stable core components for 10 years
Anti blocking, anti-corrosion and extended maintenance
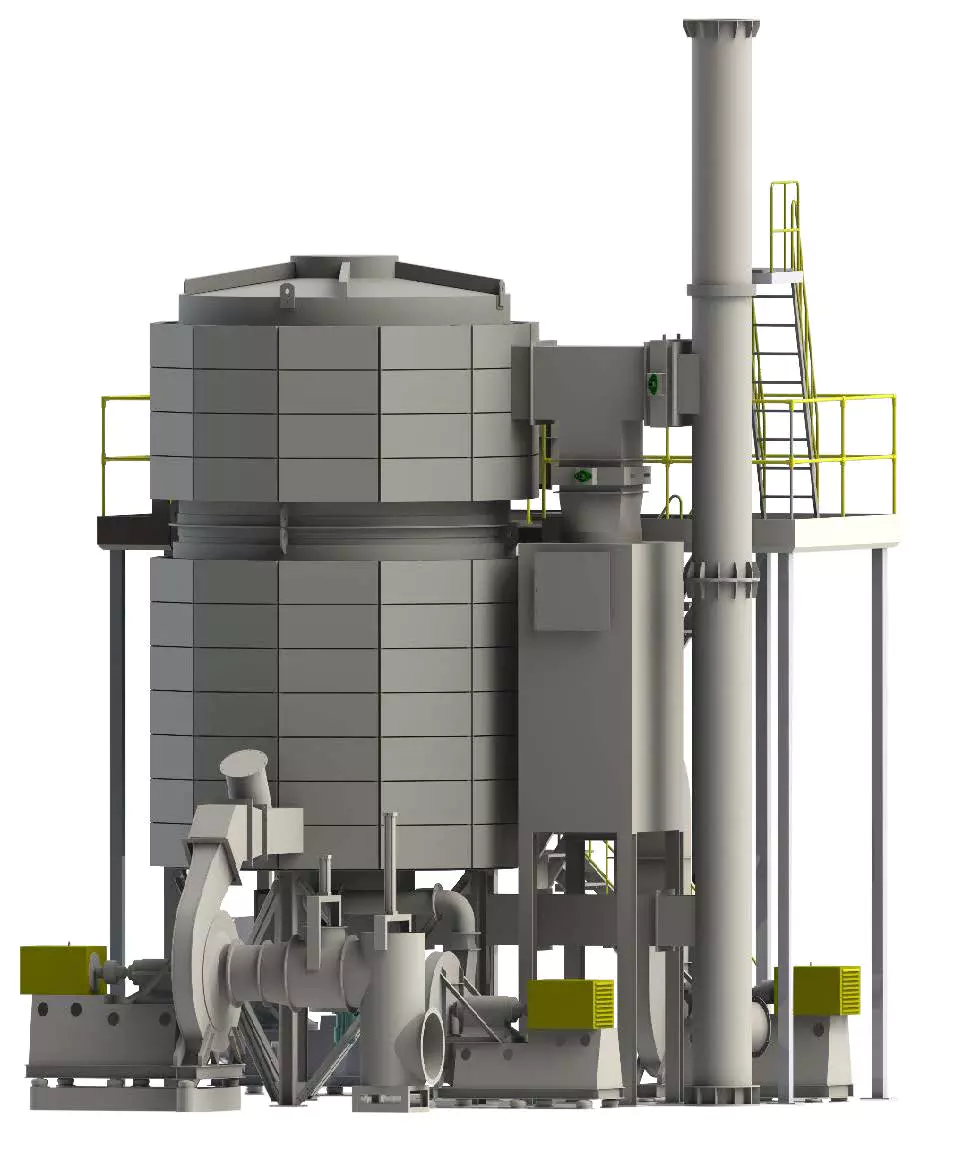
Choice of RTO Regenerative Thermal Oxidizers
3-chambers RTO (3 chambers)
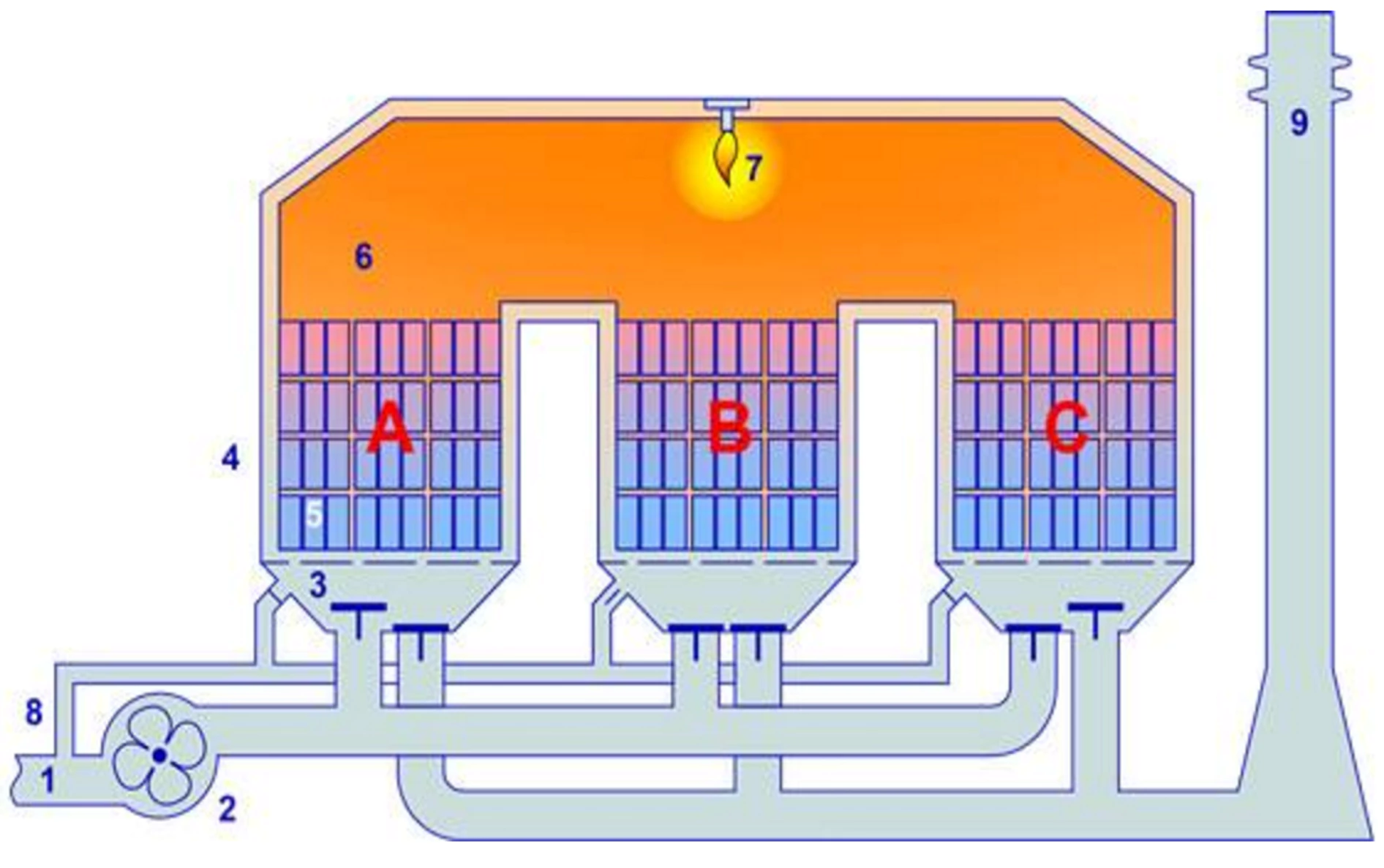
The three-chamber RTO has high exhaust temperature, high energy consumption, high operating costs, and the switching valve works 520,000 times per year with a short life span.
Rotary RTO (12 chambers)
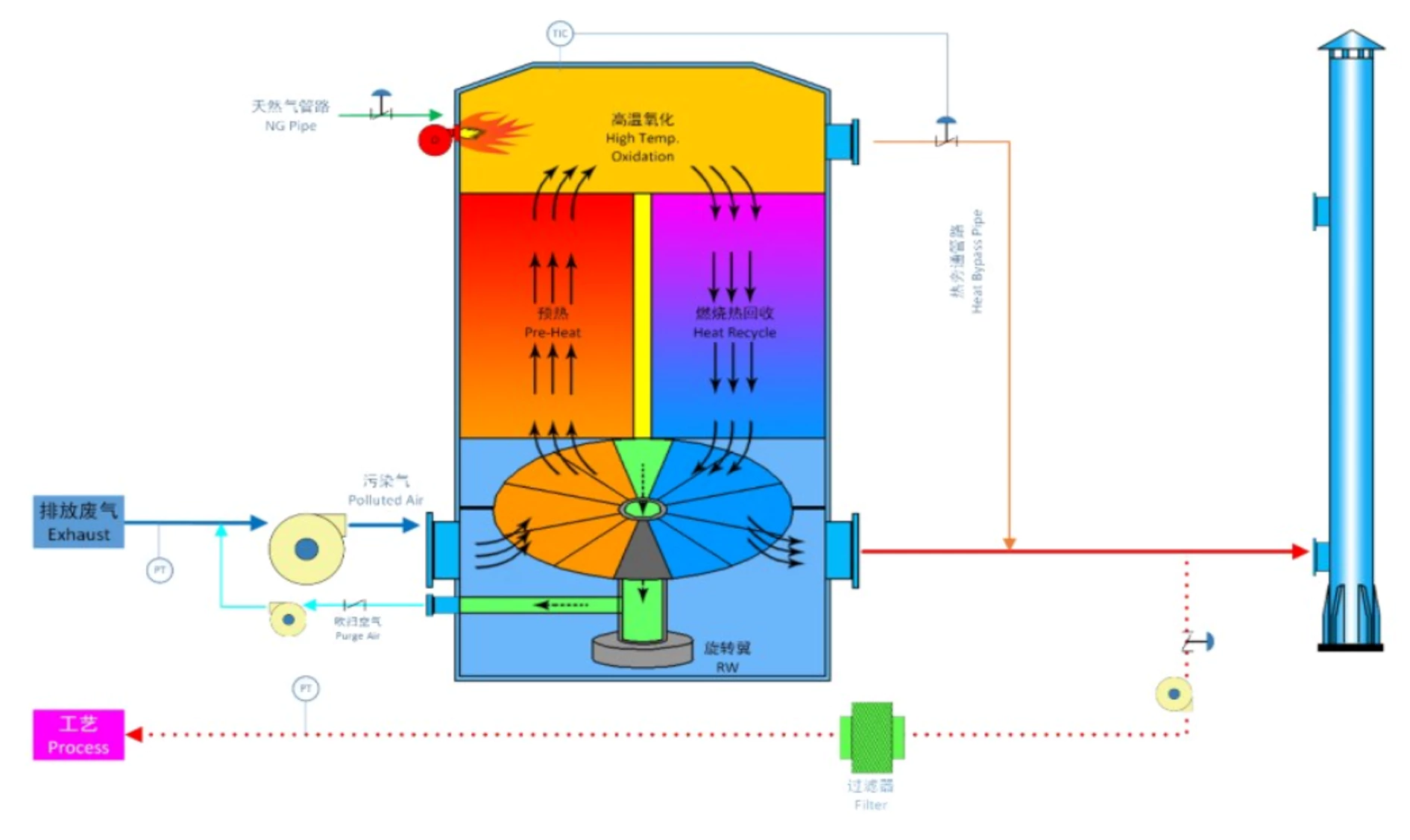
Rotary RTO exhaust temperature is less than 80 degrees and has low energy consumption, low operating costs, continuous operation of the rotary valve without switching, and long service life.
Solve the problem of ultra high heat storage rate
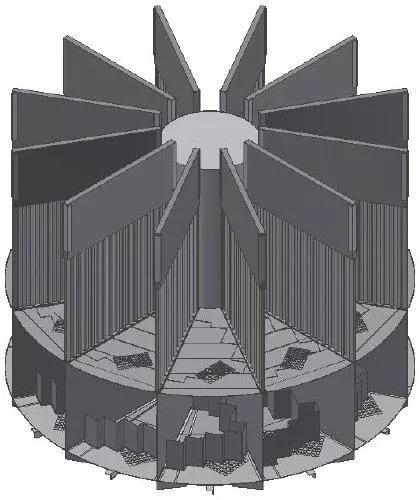
Diaphragm form
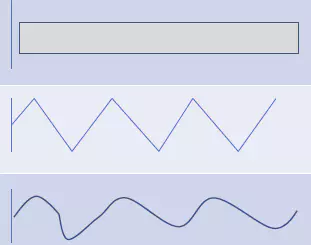
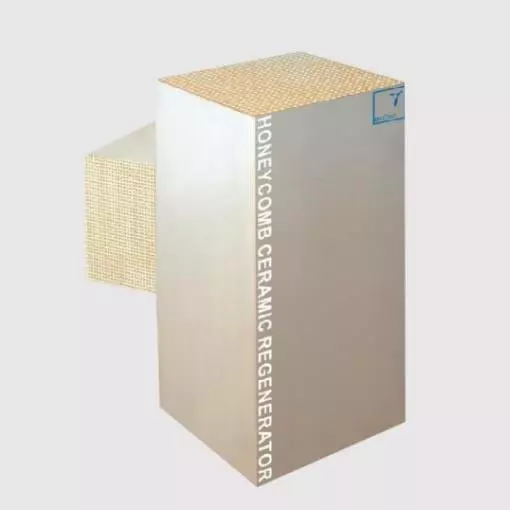
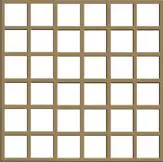

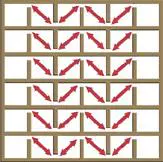
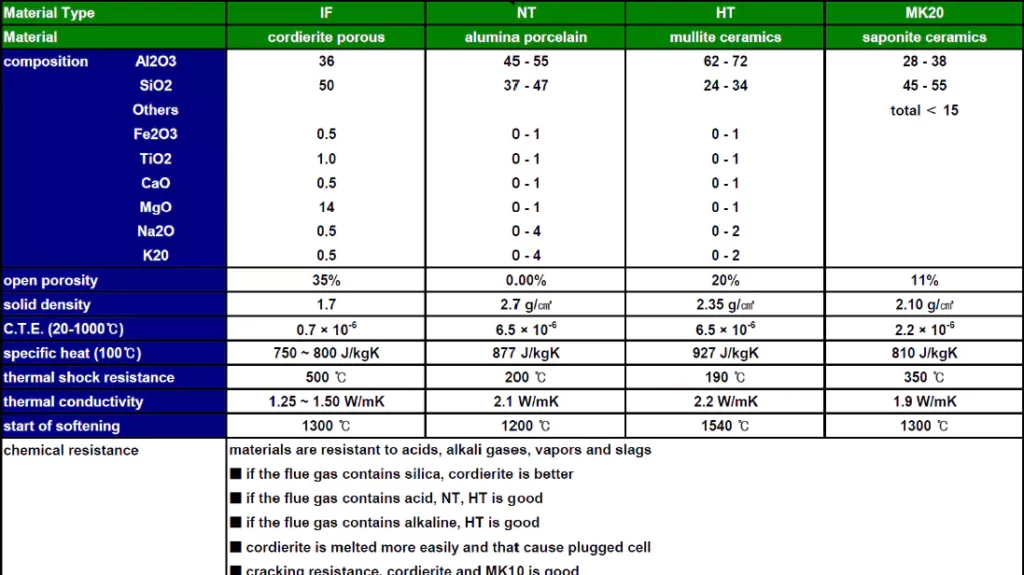
Solve the problem of ultra high heat storage rate
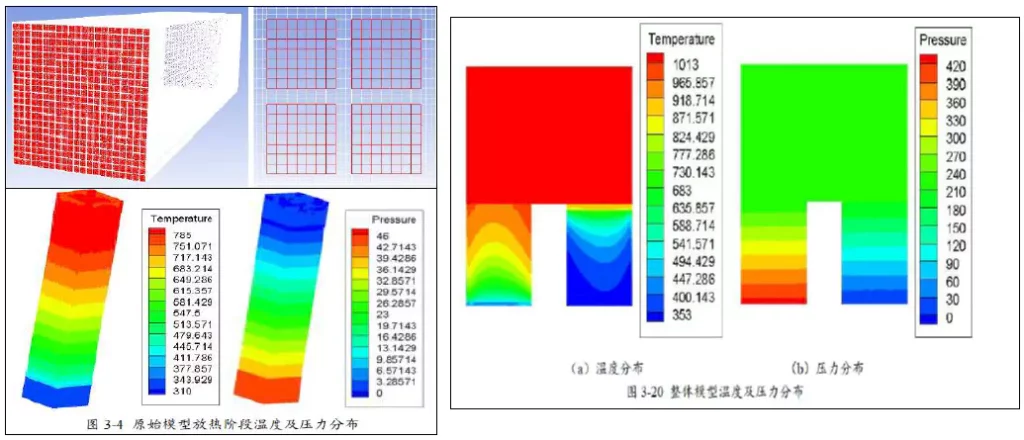
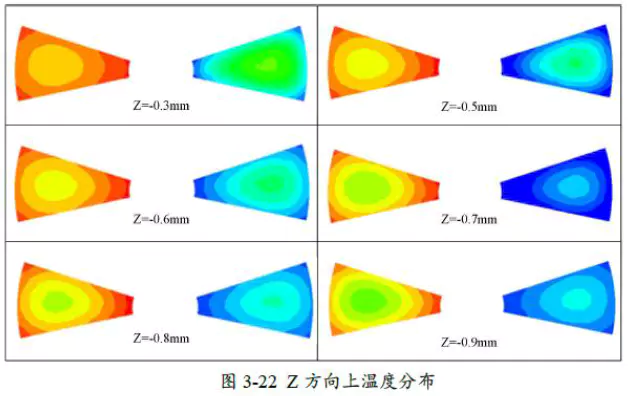
Temperature distribution in the Z direction
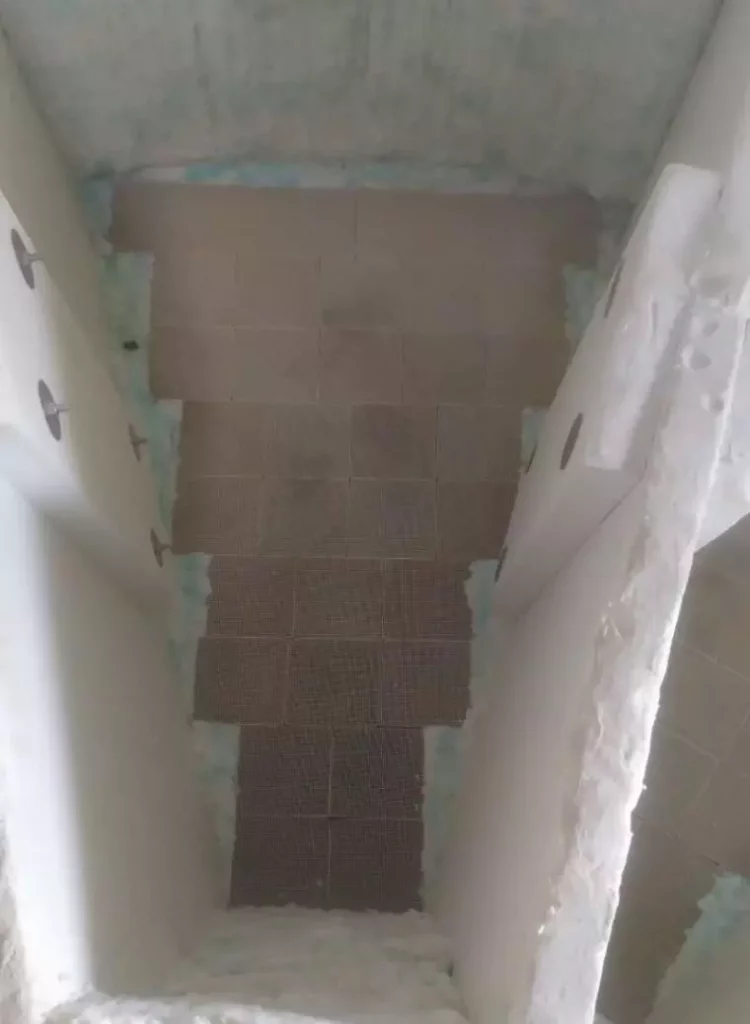
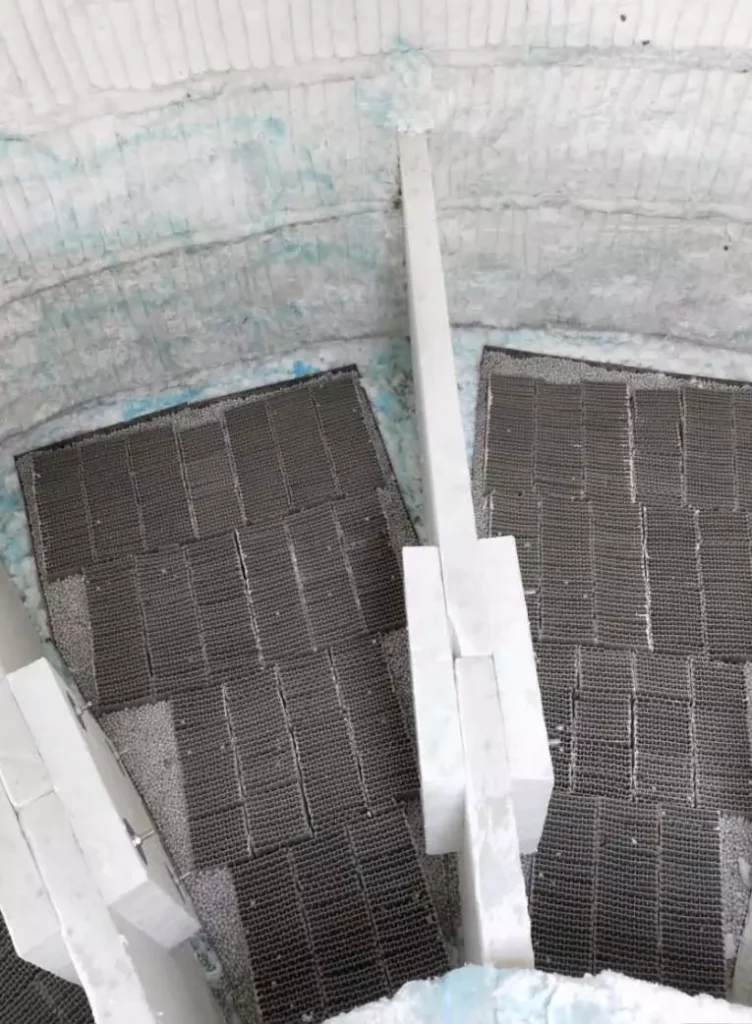
Installation process of insulation cotton
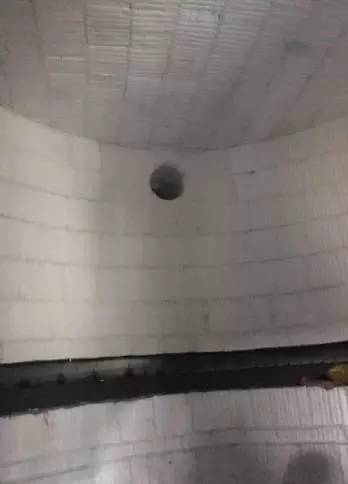

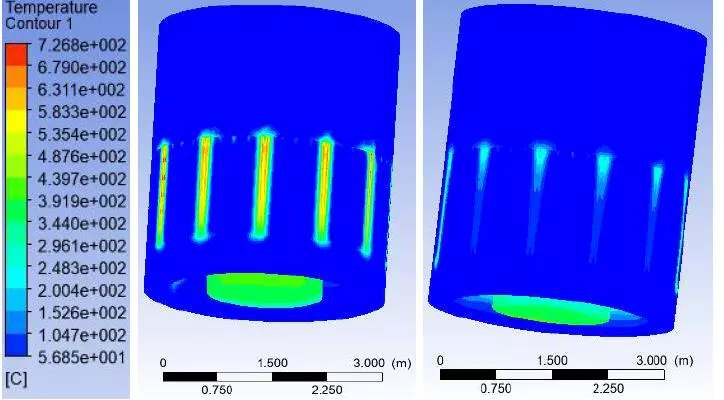
Insulation shell
Thermal insulation and energy-saving performance
A vacuum insulation shell is designed on the surface of ” Toptank ” RTO furnace body to reduce convection heat dissipation
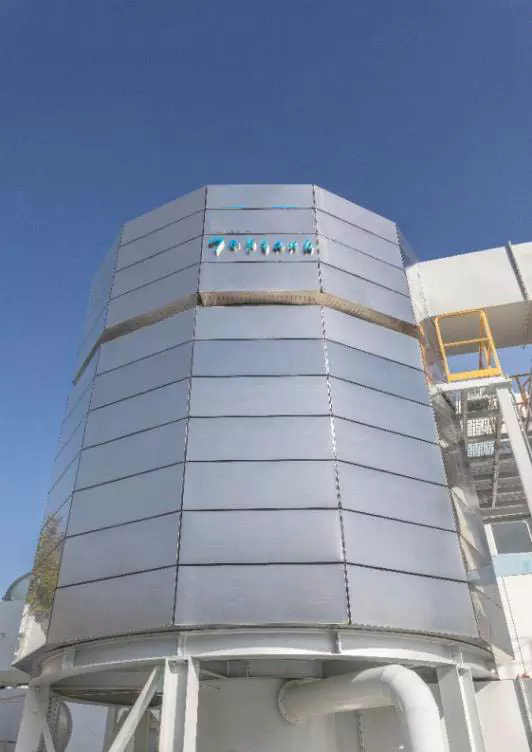
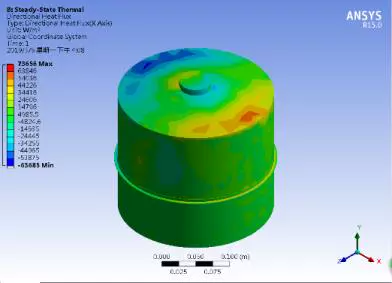
The simulation of the
temperature field of heat
loss in the windward face of
the outer surface of the
common RTO furnace shows
that the heat loss is 1.4×10 4
W/m 2
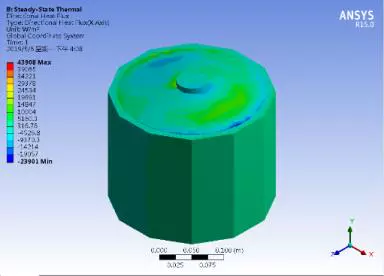
The heat loss of the
outer shell of
Toptank RTO furnace
body is 0.5x 10 4
W/m 2
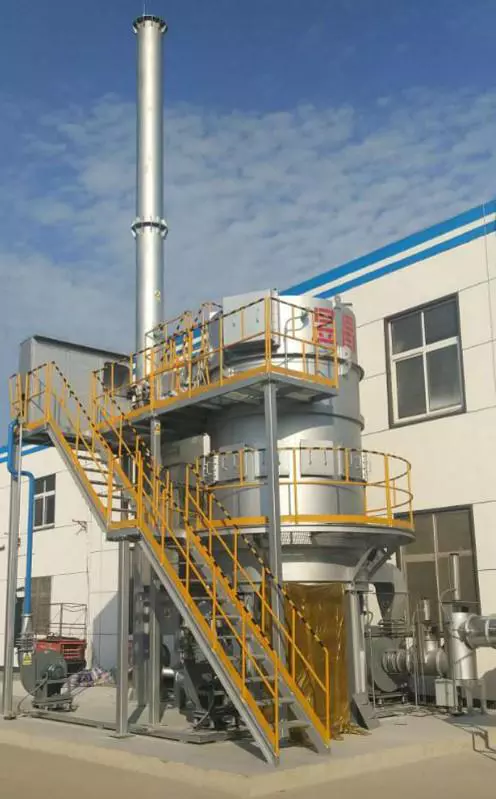
Solve the service life and stability of core components
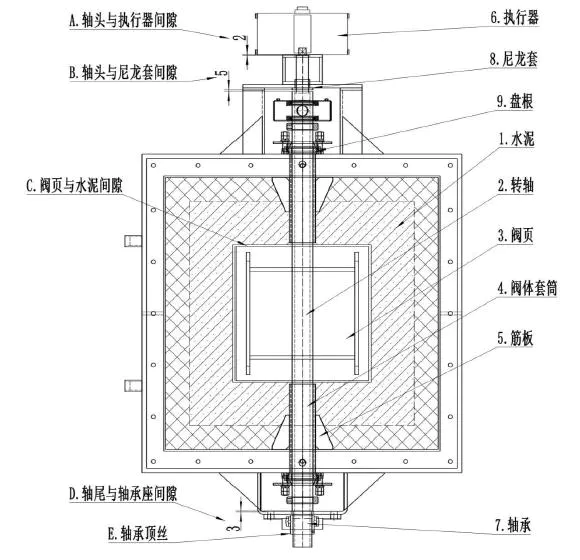
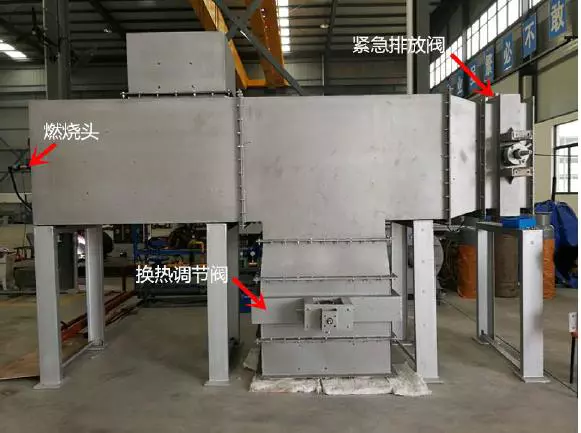
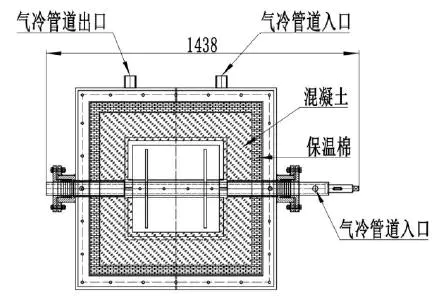
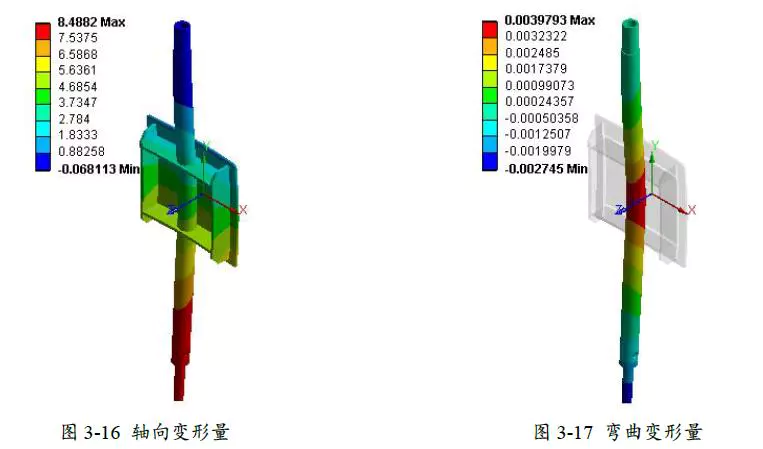
Axial deformation | Bending deformation |
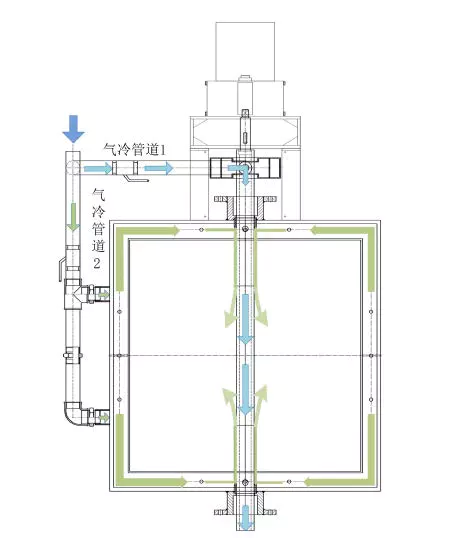
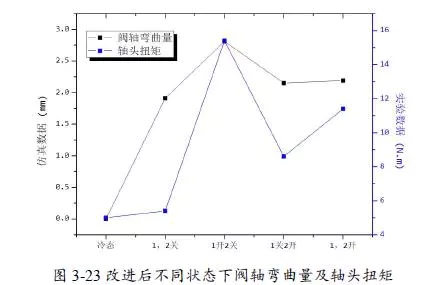
After improvement, the valve shaft bending amount and shaft head torque in different states
Rotary valve seal
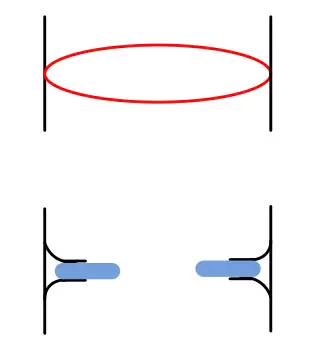
lip seal
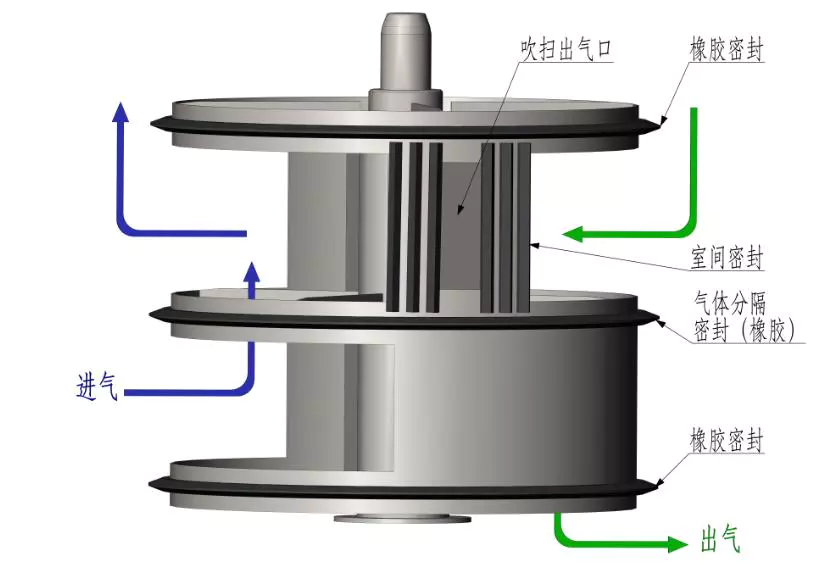
Regenerative Thermal Oxidizer Advantage – Recovery of Waste Heat
1. Recovery of waste heat through steam
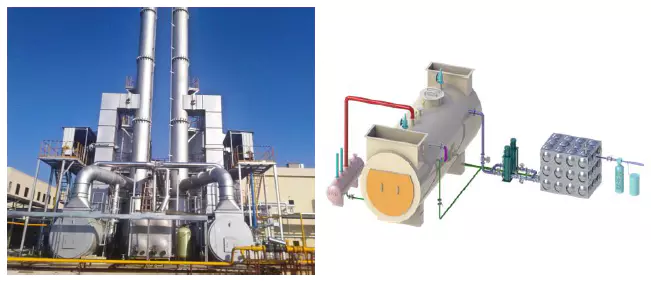
2. Recovery of waste heat through hot water
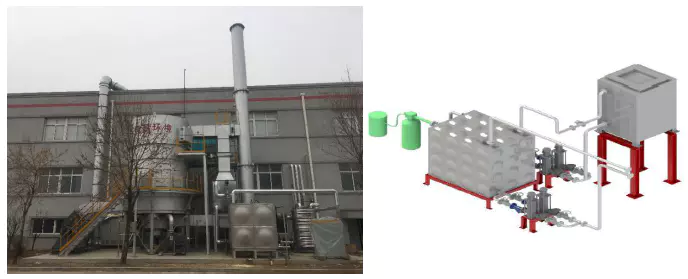
3. Recovery of waste heat through conduction oil
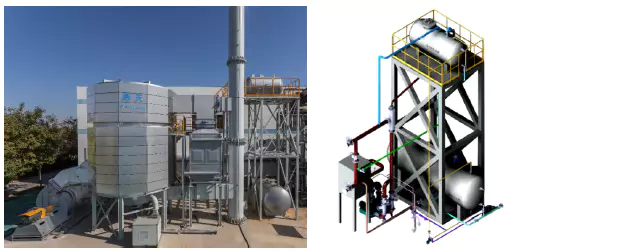
4. Recovery of waste heat through hot wind
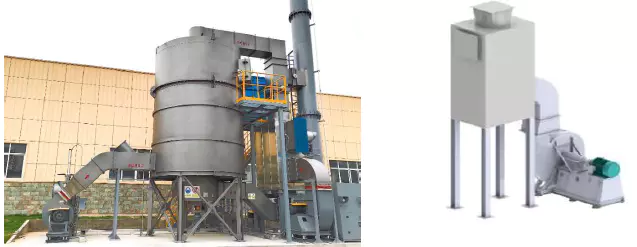
Cloud service system
Internet of things big data interconnection Remote monitoring, remote diagnosis, fault troubleshooting, maintenance reminder, data recording, and other functions in one, to provide customers with high quality and efficient value-added services.
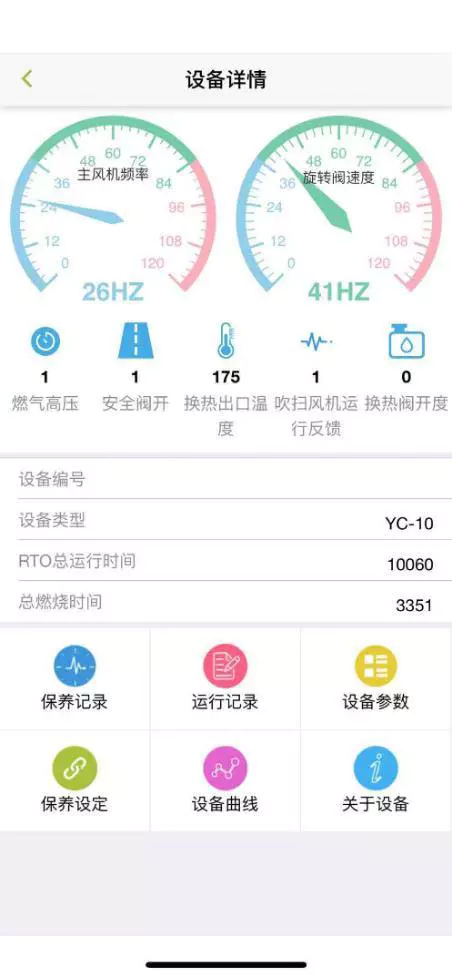
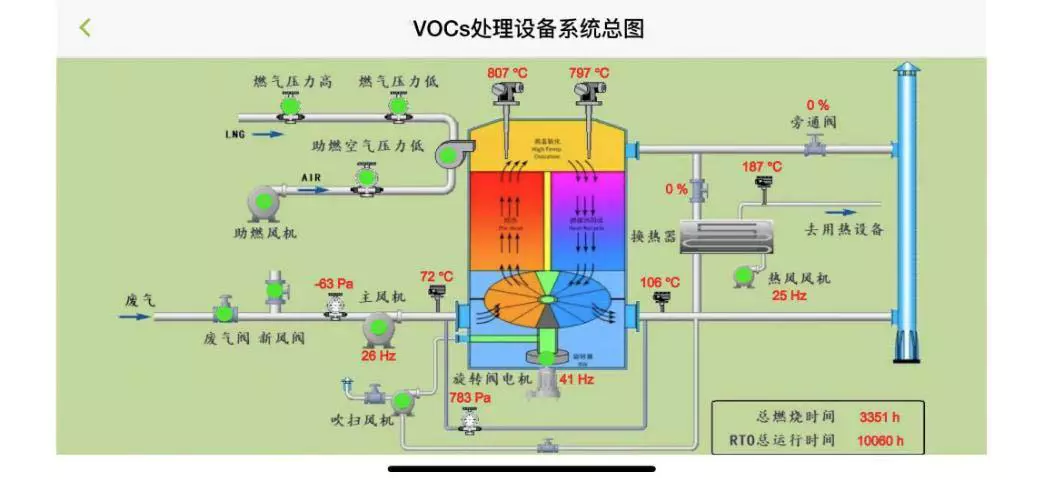
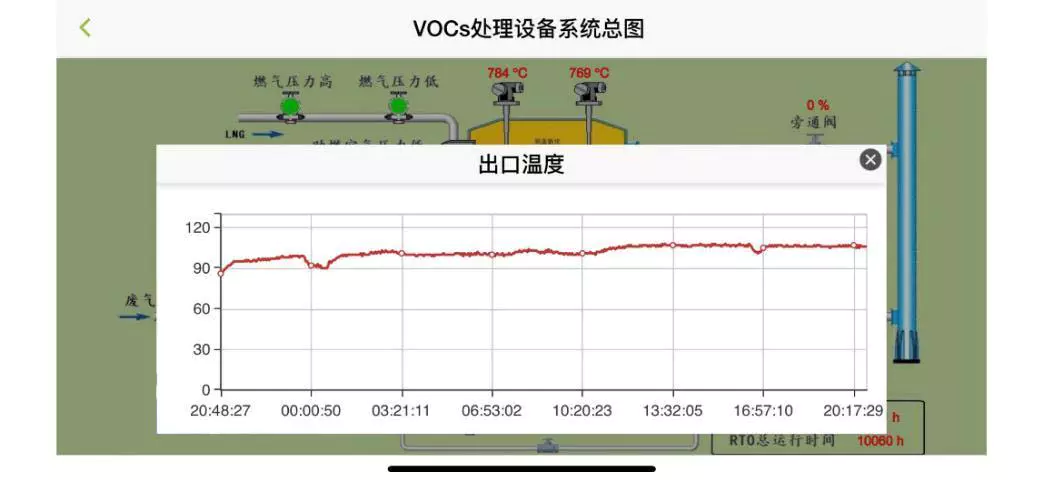
Regenerative Thermal Oxidizer Marketing and Application
General situation of project signing
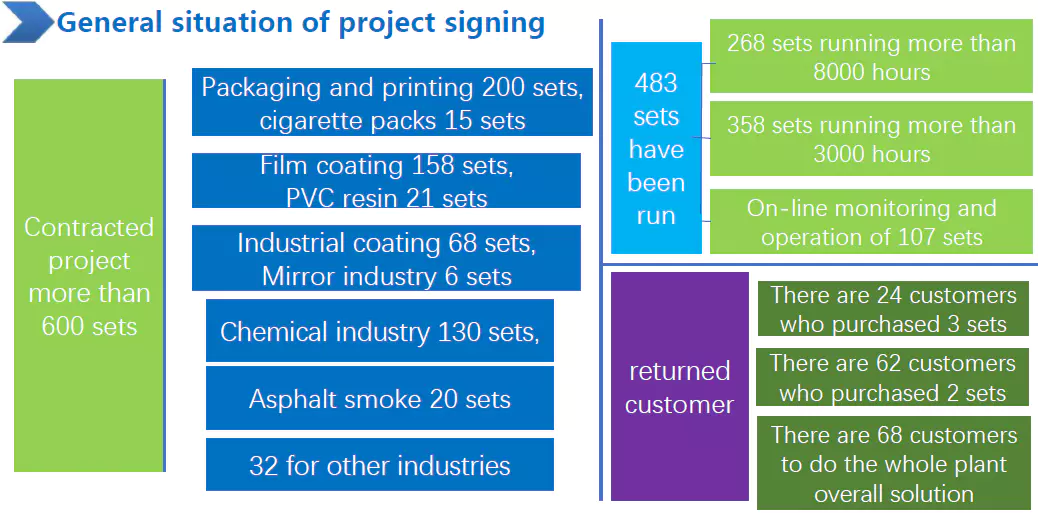
Application cases
Whole plant solution
Equipment configuration:
- 3x40000Nm³/h-RTO
- 1000000Nm³/h-Zeolite rotor
- 3x6t/h-2.0MPa Steam boiler
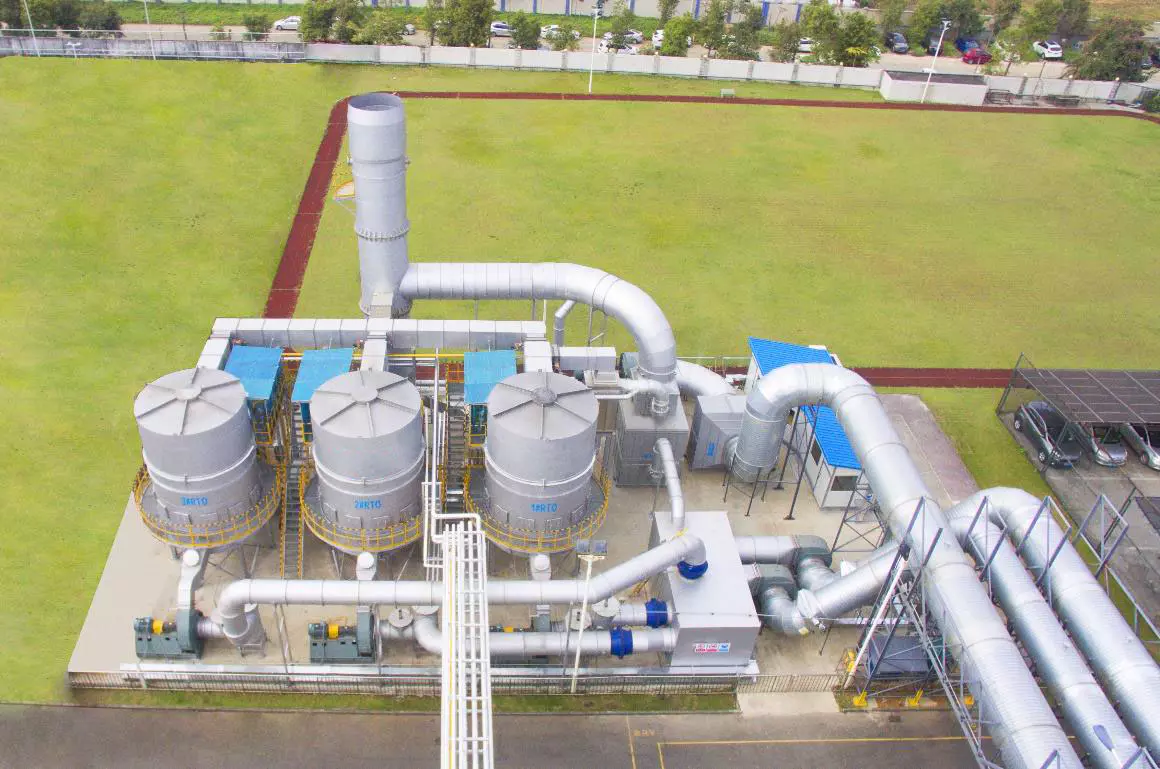
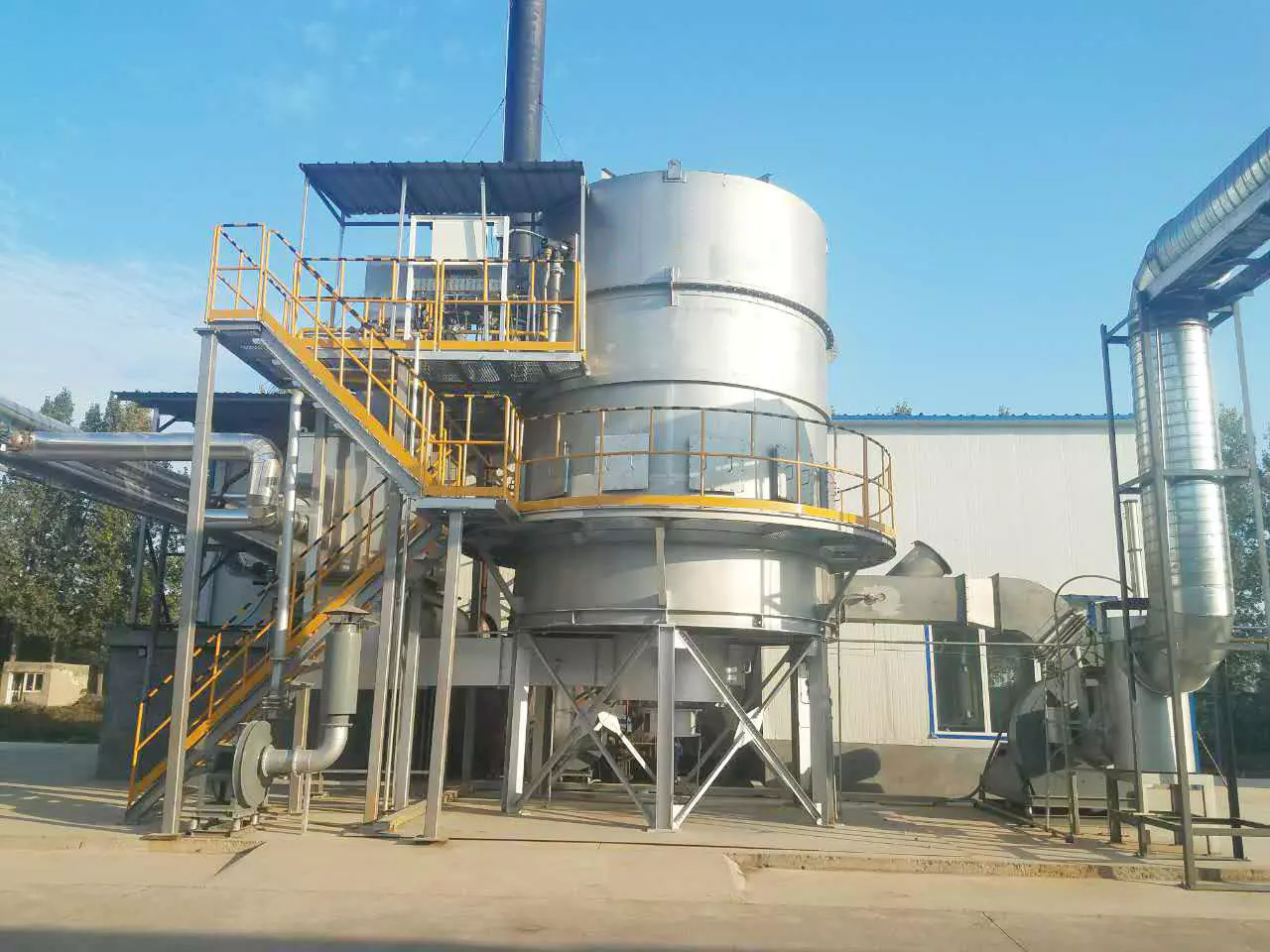
High concentration waste gas solution
Equipment configuration:
- 30000Nm³/h-RTO
- 6t/h-heat conducting oil boiler
Project | Index |
Concentration | 8600mg/m³ |
Volume | 30000Nm³/h |
Composition | Ethyl ester, toluene |
Purification efficiency | 99.62% |
Emission limit | 28.8mg/m³ |
Low concentration solution
Equipment configuration:
- 10000Nm³/h-RTO
- 80000Nm³/h-Zeolite rotor
Project | Index |
Concentration | 620mg/m³ |
Volume | 80000Nm³/h |
Composition | Xylene, butyl |
Purification efficiency | 96.1 % |
Emission limit | 24.18mg/m³ |
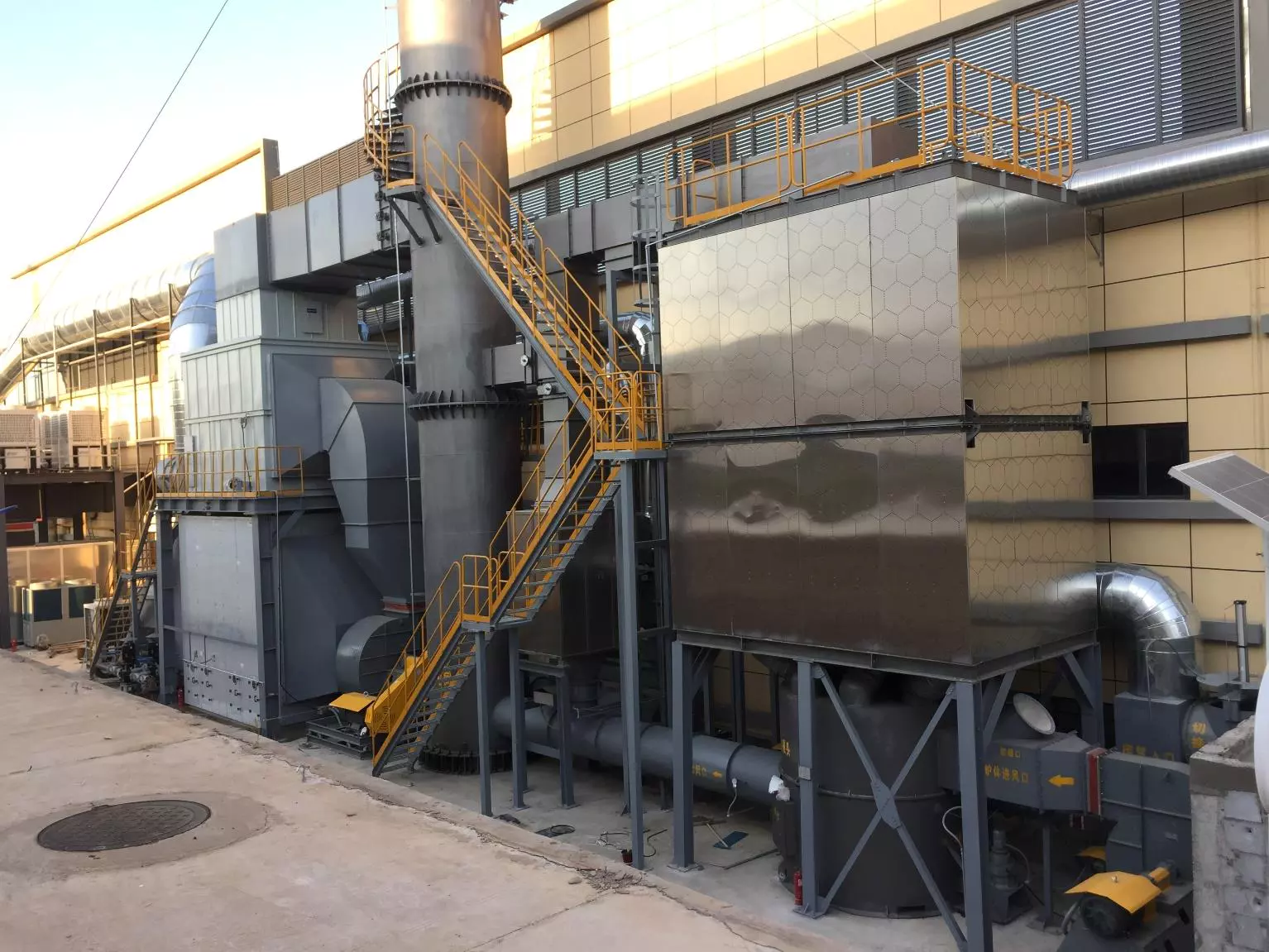
Solutions for complex chemical waste gas
Organic waste gas: Alkanes, olefins, alkynes, aromatic aldehydes, ketones, ethers, sulfur/chlorine/nitrogen organics
Accompanying components: H2S, SO2HCl CO, NH3
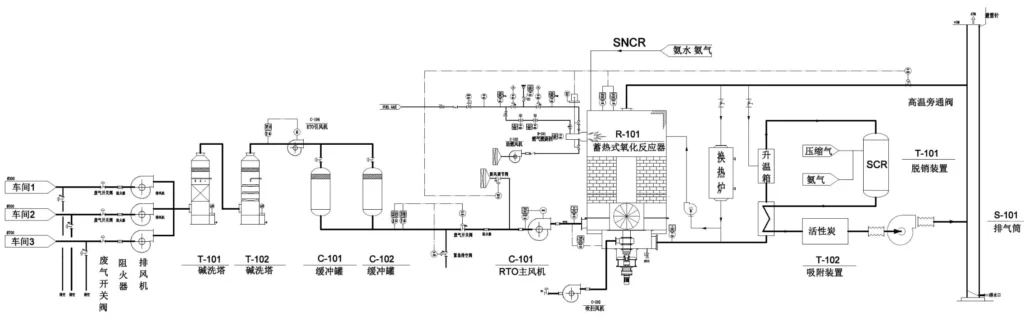
Difficulty | Measures | Difficulty | Measures |
Corrosive gas | Alkaline washing, pickling, dehumidification, Corrosion resistant material, Anticorrosive coating | NOx | SNCR/SCR Denitration |
Concentration surge | Buffer tank, FTA concentration peak remote warning | Viscous polymer | Plate type heat storage ceramic and 12 manholes for maintenance |
dioxin | activated carbon adsorption | waste heat | Hot air recovery |
Waste gas solution of the sewage tank
Waste gas components:
- Ammonia, hydrogen chloride, xylene Ammonia content 20%
- The lower explosion limit Process composite of ammonia is 15%
Process composition:
- Spray tower +RTO+SCR
- 10000Nm³/h RTO
- 50000Nm³/h RTO
Features:
- Chlorine and corrosion-resistant materials
- NOx emission control
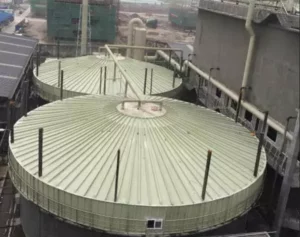
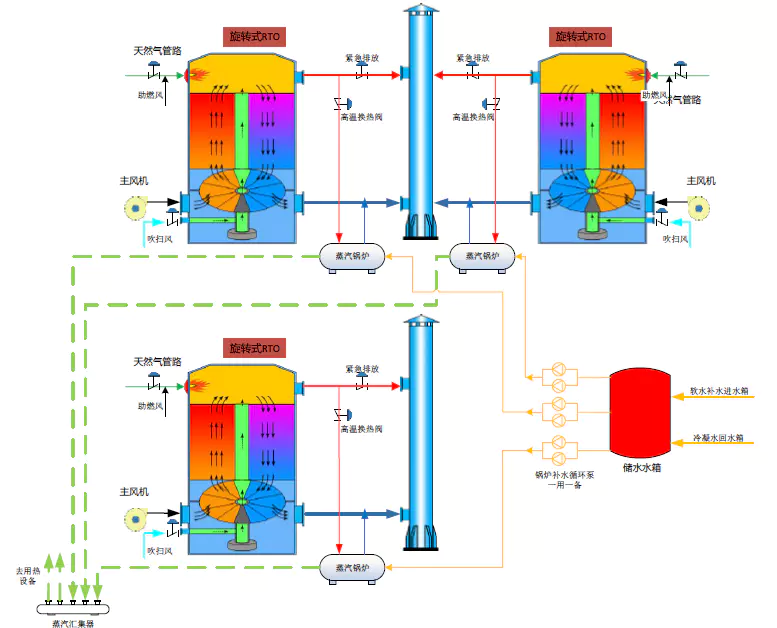
Thermal energy utilization solutions
Equipment configuration:
- 3x40000Nm³/h-RTO
- 3x8t/h-2.0MPa boiler
- 3000KW Steam type lithium
- bromide refrigerator
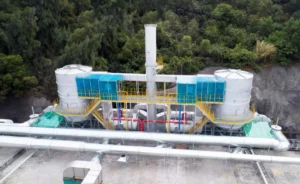
Concentration surge solutions
Features:
Concentration surge, chlorine-containing
corrosion, amine-containing
Waste gas components:
3-methylpyridine, 3-cyanopyridine, 3-aminopyridine, methanol, toluene, ethanol, triethylamine, chloroform, short chain fatty acids, aliphatic hydrocarbons, ammonia and trichloroethylene
Process composition:
Concentration fluctuation pretreatment + RTO corrosion prevention + post-treatment to remove hydrogen chloride and dioxin
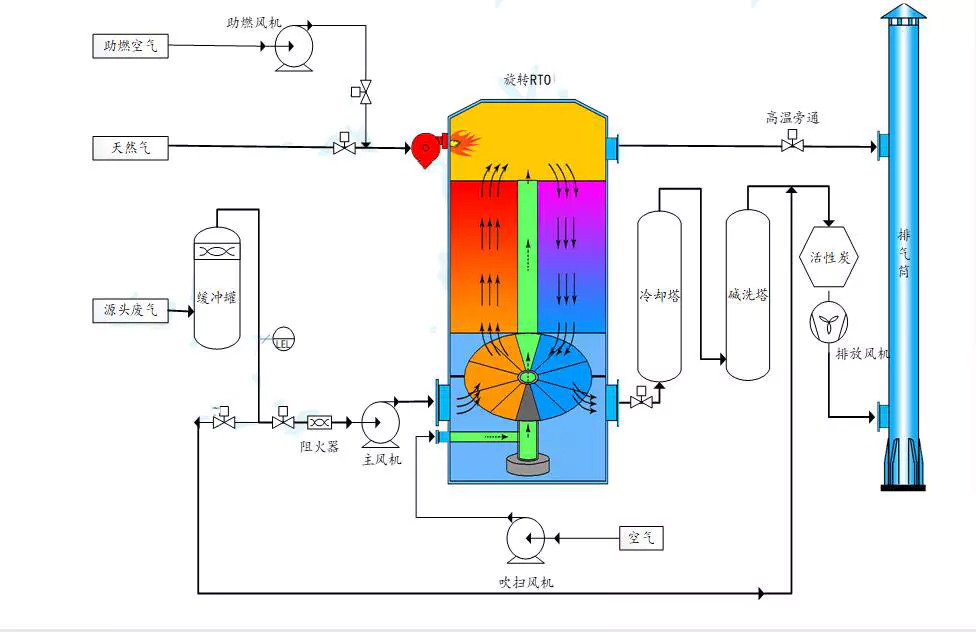
Equipment configuration:
- 2x40000Nm³/h-RTO
Waste gas pipeline
Pretreatment system
Asphalt fume solution
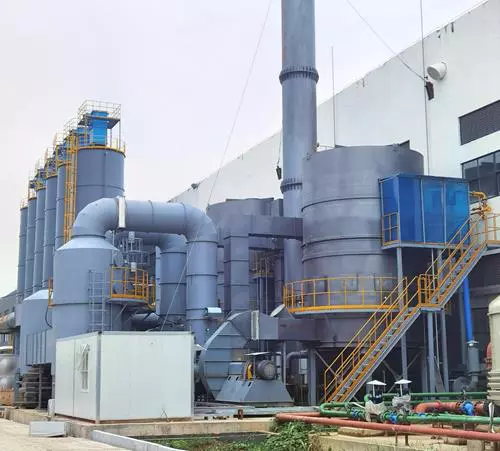
Features:
High boiling point lipid aerosol, Dust
Process composition:
- Pipe heat tracing
- Oil drain
- Fire fighting system
- Cyclone filter
- Screen filter
- Quick replacement of Bottom heat storage ceramic
Regenerative Catalytic Oxidizer
The Regenerative Catalytic Oxidizer (RCO) system is based on the structure of an RTO, with a special catalyst material added to the oxidizer, which provides enough heat energy to destroy VOCs to lower the operating temperature of the RTO system and increase the rate of oxidation reaction. Unlike thermal combustion, RCO is flameless and automatically shuts down the heater when the treatment inlet gas exceeds 300°C. It is widely used because it is environmentally friendly and energy efficient.
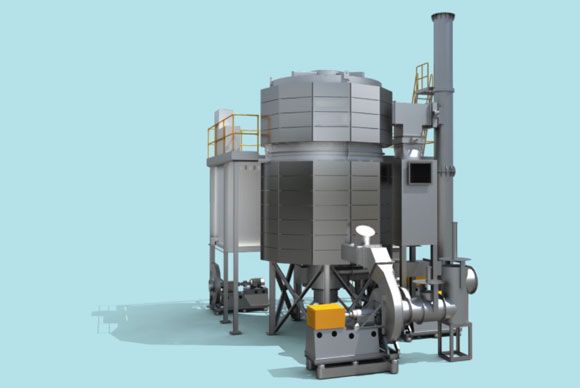
Regenerative Thermal Oxidizer VS Thermal Oxidizer
Thermal oxidizers are used in a variety of industrial applications and are a preferred technology in the field of air pollution control. Their efficiency and durability make them an excellent choice for many processes. Advanced thermal oxidizer systems are particularly advantageous in air pollution control applications, where they are used to effectively destroy hazardous air pollutants and volatile organic compounds. They are also environmentally friendly and meet stringent environmental regulations.
Regenerative Thermal Oxidizers use a ceramic heat exchanger to heat up the exhaust gas in a controlled environment. The heated air then enters a combustion chamber, where it is preheated to a set temperature. Once heated, this clean air is then exhausted through a stack into the environment. Regenerative thermal oxidizers (RTO) are the excellent choice for any chemical plant and can significantly reduce operating costs, particularly when combined with an effective heat recovery system.
Recuperative Thermal Oxidizer VS Regenerative Thermal Oxidizer
The primary difference between a recuperative thermal oxidizer and a regenerative thermal oxidizer is the way in which the technology recovers energy.
A recuperative thermal oxidizer uses a heat exchanger to convert exhaust gas into useful heat. This heat can then be used to heat the incoming air. Both types of oxidizers can have multiple heat recovery devices.
Regenerative thermal oxidizers require more complicated technology than recuperative thermal oxidizers. They utilize valves that reverse the airflow and ceramic heat sinks that absorb heat from the hot air. The heated air then passes through a combustion chamber where VOCs are oxidized.
Regenerative thermal oxidizers are more versatile and efficient. Their high efficiency can make them ideal for long-running operations and high-VOC concentrations. They use ceramic media to capture heat and are more energy efficient. They are also a great choice for low-VOC concentrations.