Regenerative Thermal Oxidizer
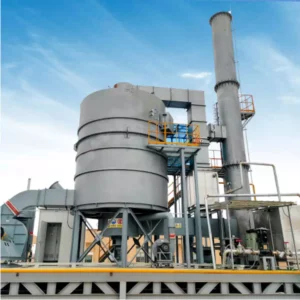
Through the typical rotary RTO
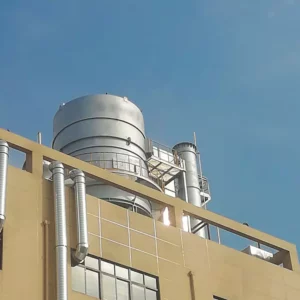
Standard rotary RTO
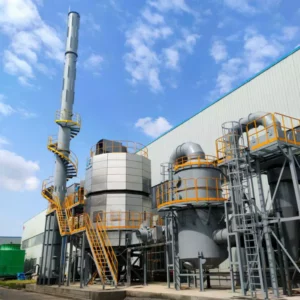
Toptank rotary RTO
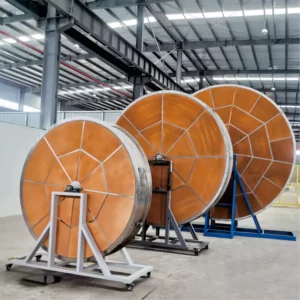
Thermal oxidizer combined with VOC concentrator
company profile
Ever-Power Pte. Ltd. is a high-end equipment manufacturing high-tech enterprise focusing on the comprehensive treatment of volatile organic compounds (VOCs) exhaust gas and carbon emission reduction and energy-saving Technology, with heat energy, combustion, sealing, automatic control four core technologies; Capable of temperature field simulation and air flow field simulation and modeling; With ceramic thermal storage material performance, zeolite molecular sieve adsorption material comparison and selection, VOCs organic matter high-temperature incineration oxidation characteristics of experimental testing ability. The regenerative thermal oxidizers we manufacture help enterprises to successfully embark on the road to green development, to achieve economic development and environmental protection win-win situation.
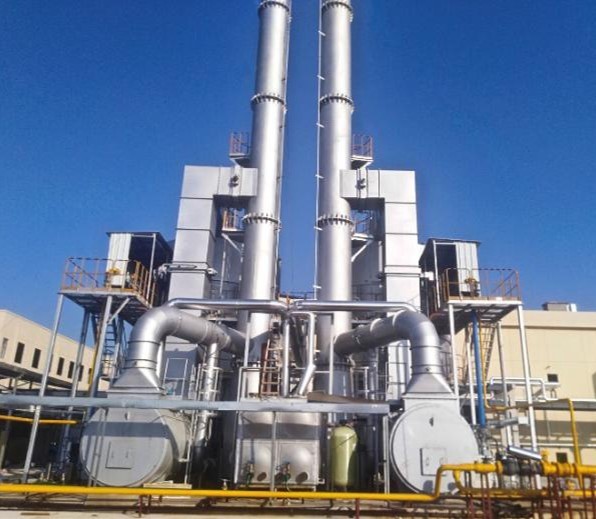
We have applied for 68 patents on core technologies, including 21 invention patents, and the patented technologies basically cover key components.
Among them, we have been authorized: 4 invention patents, 41 utility model patents, 6 appearance patents, and 7 software copyrights.

Our Honors and Qualifications

Excellent Manufacturing Capabilities
Annual production of 300 sets of RTO equipment and 60 sets of zeolite molecular sieve rotors! Strict ISO9001 quality management system, standardized production process, batch manufacturing, core parts production are all mastered by ourselves, professional self-owned engineering delivery, commissioning and after-sales service team. Known as “the world’s first brand of RTO furnace“

Automatic Shot Blasting & Painting Production Line For Steel Plates & Profiles
Manual Shot Blasting Production Line
Dust Removal & Environmental Protection Equipment
Automatic Spray Paint Room
Drying Room
Full-process high-quality parts production

Regenerative Thermal Oxidizers
RTO Application
Regenerative Thermal Oxidizers(RTO) are widely used in the following industries:
Petrochemical industry, Storage and transportation operations, Organic Chemicals, paint manufacturing, rubber manufacturing, Packaging and Printing, car spray, Ship spraying, Container spraying, furniture manufacturing, Semiconductor Industry, leather manufacturing, shoe industry, Textile, sewage treatment.



SERVICE PROCESS
Project Research
Collect customer’s exhaust gas parameters, make preliminary planning of equipment configuration and specifications based on customer’s basic requirements.
Project Evaluation
To the customer site for product technology exchanges, a preliminary survey of the project site, and a comprehensive investigation, in order to more scientific and comprehensive scheme design
conceptual design
According to the detailed exhaust gas parameters and combined with the customer’s production process, the system design engineer will plan the overall process plan of the project, product configuration, quality control, manufacturing schedule, delivery schedule, etc
Technical Exchange
According to the specific plan, conduct detailed and comprehensive in-depth communication with customers on the process PID flow chart, safety measures, related standards and project configuration, to ensure the rigorous implementation and execution of the plan
Sign a Contract
On the premise that the project plan and budget are determined by both parties, a contract shall be signed to clarify the rights and obligations of both parties
Project Implementation
According to the final scheme, professional design team, production team and engineering team are configured to fully carry out the implementation of engineering projects, and supervise and control all links such as manufacturing, transportation, installation, commissioning and training
Acceptance of delivery
The customer system design engineer, project manager and other joint project quality acceptance and delivery
Follow-up Service
Overall filing of engineering project materials, equipped with professional after-sales service team to track project operation services and provide technical support