Regenerative Thermal Oxidizer Case Studies
Introduction
Regenerative Thermal Oxidizers (RTOs) are widely used in various industries to control air pollution and reduce emissions. In this article, we will explore several case studies that highlight the effectiveness and benefits of RTOs in different applications. Each case study will provide a comprehensive overview of the specific industry, the challenges faced, and how an RTO was implemented to address those challenges.
Case Study 1: Industrial Manufacturing
– The industrial manufacturing sector often deals with high levels of volatile organic compounds (VOCs) emissions.
– Case study overview: A leading manufacturing company faced compliance issues due to VOC emissions exceeding regulatory limits.
– Implementation of an RTO: The company installed an RTO system to treat the exhaust gases, efficiently destroying VOCs through thermal oxidation.
– Results and benefits: The RTO successfully reduced VOC emissions, ensuring compliance with environmental regulations while improving air quality and minimizing operational costs.
Case Study 2: Petrochemical Industry
– Petrochemical plants produce a wide range of hazardous pollutants, including volatile organic compounds (VOCs) and nitrogen oxides (NOx).
– Case study overview: A petrochemical facility experienced challenges in meeting stringent emission standards and faced potential penalties.
– Implementation of an RTO: The facility installed an advanced RTO system equipped with ceramic media beds and energy recovery technology.
– Results and benefits: The RTO efficiently destroyed VOCs and NOx, achieving compliance with emission regulations. It also significantly reduced energy consumption and provided cost savings for the facility.
Case Study 3: Pharmaceutical Sector
– Pharmaceutical processes involve the release of volatile organic compounds (VOCs) and hazardous air pollutants (HAPs).
– Case study overview: A pharmaceutical company sought a solution to control emissions and maintain product quality.
– Implementation of an RTO: The company integrated a customized RTO system with a comprehensive air pollution control strategy.
– Results and benefits: The RTO effectively eliminated VOCs and HAPs, ensuring compliance with strict industry regulations. Additionally, it enhanced product quality and reduced the company’s carbon footprint.
Case Study 4: Food Processing
– Food processing facilities generate odorous compounds and particulate matter, which pose challenges in odor control and air quality.
– Case study overview: A food processing plant faced community complaints regarding unpleasant odors and potential health risks.
– Implementation of an RTO: The plant installed an RTO system with a specialized odor control unit to address the odor and air quality concerns.
– Results and benefits: The RTO successfully removed odorous compounds, improving community relations, and maintaining a safe and hygienic working environment.
Conclusion
Regenerative Thermal Oxidizer case studies demonstrate the versatility and effectiveness of RTO systems in various industries. The provided examples highlight how RTOs help businesses achieve regulatory compliance, reduce emissions, improve air quality, and enhance operational efficiency. By adopting RTO technology, industries can contribute to a cleaner and more sustainable environment while ensuring their continued success.
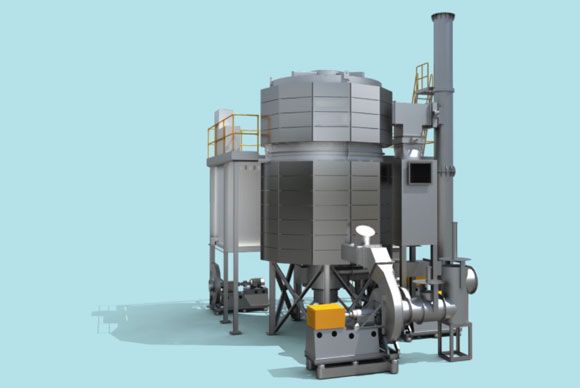
Company Introduction
We are a high-tech equipment manufacturing enterprise specializing in the comprehensive treatment of volatile organic compounds (VOCs) and carbon reduction and energy-saving technologies. Our core technologies include four major areas: thermal energy, combustion, sealing, and automatic control. We have the ability to simulate temperature fields, air flow fields, and VOCs organic high-temperature incineration oxidation characteristics. Our team consists of over 360 employees, including more than 60 R&D technology backbones, 3 senior engineers, 6 senior engineers, and 24 thermodynamics doctors. Our core products include rotary valve regenerative thermal oxidizers (RTOs) and zeolite molecular sieve adsorption concentration rotors, which combined with our own environmental protection and thermal energy system engineering expertise, can provide customers with comprehensive solutions for industrial waste gas treatment and carbon reduction integrated solutions.
Team Advantage: We have established RTO technology development center and waste gas carbon reduction engineering technology center in Xi’an and a 30,000 square meter production base in Yangling, and we are the leading manufacturer of RTO equipment and zeolite molecular sieve rotary equipment worldwide. Our core technical team comes from the Aerospace Liquid Rocket Engine Research Institute (Aerospace Sixth Academy).
Certifications, Patents, and Honors
- Intellectual Property Management System Certification
- Quality Management System Certification
- Environmental Management System Certification
- Construction Enterprise Qualification
- High-tech Enterprise
- Rotary Valve Regenerative Thermal Oxidizer Patent
- Rotary Heat Storage Incinerator Rotor Patent
- Plate Zeolite Rotary Patent, etc.
How to Choose the Right RTO Equipment
- Understand your waste gas composition and process flow.
- Determine the volume and temperature of the waste gas treated per hour.
- Select the appropriate RTO equipment based on the waste gas composition and volume.
- Determine the installation location of the RTO equipment and the length of the duct.
- Choose the right control system based on the processing requirements of the waste gas.
Please note that each point requires further explanation tailored to the specific needs of the customer.
Our Service Process
- Consultation and Evaluation: Preliminary consultation, on-site inspection, and demand analysis.
- Design and Plan Development: Scheme design, simulation and modeling, and scheme review.
- Production and Manufacturing: Customized production, quality control, and factory testing.
- Installation and Commissioning: On-site installation, commissioning, and training services.
- After-sales Support: Regular maintenance, technical support, and spare parts supply.
We are a one-stop solution with a professional team that can tailor an RTO solution to the specific needs of the customer.