How to clean an RTO for air pollution control?
Introduction
Cleaning a Regenerative Thermal Oxidizer (RTO) is essential for efficient air pollution control. An RTO is a widely used system in industrial facilities for reducing emissions of volatile organic compounds (VOCs) and hazardous air pollutants (HAPs). Regular cleaning and maintenance ensure optimal performance and compliance with environmental regulations. This article will discuss various aspects of cleaning an RTO for air pollution control.
Why is RTO cleaning important?
- Removal of particulate matter: Cleaning an RTO helps remove accumulated particulate matter from the heat exchangers, reducing the risk of clogging and improving heat transfer efficiency.
- Prevention of fouling: Regular cleaning prevents fouling, which can lead to decreased performance and increased energy consumption.
- Minimization of corrosion: Cleaning the RTO’s surfaces and components prevents corrosion, ensuring longer equipment lifespan and reliable operation.
Methods for cleaning an RTO
There are several methods available for cleaning an RTO, including:
1. Mechanical cleaning
Mechanical cleaning involves physically removing the accumulated deposits from the RTO’s surfaces using brushes, scrapers, or high-pressure water jets. This method is effective in removing heavy deposits and stubborn contaminants.
2. Chemical cleaning
Chemical cleaning utilizes specialized cleaning agents to dissolve and remove contaminants from the RTO. This method is particularly useful for removing organic deposits and complex fouling.
3. Steam cleaning
Steam cleaning involves directing high-temperature steam onto the RTO’s surfaces to dissolve and dislodge contaminants. This method is effective for removing oily or greasy deposits.
Best practices for RTO cleaning
To ensure effective cleaning of an RTO for air pollution control, it is important to follow these best practices:
1. Regular cleaning schedule
Establish a regular cleaning schedule based on the operating conditions and the level of contamination in the RTO. This will prevent excessive buildup and maintain optimal performance.
2. Safety precautions
Before starting the cleaning process, ensure proper safety measures are in place, including wearing protective equipment and following the manufacturer’s guidelines.
3. Inspect and clean heat exchangers
Inspect and clean the heat exchangers regularly to remove any fouling or particulate matter that may hinder heat transfer efficiency.
4. Clean the combustion chamber
Thoroughly clean the combustion chamber to remove any carbon deposits or contaminants that can affect the combustion process.
5. Check and clean the valves and dampers
Inspect and clean the valves and dampers to ensure proper operation and prevent leakage, which can lead to decreased efficiency.
6. Document the cleaning process
Keep a record of the cleaning activities, including the date, method used, and any observations made during the process. This documentation will help track maintenance activities and identify any recurring issues.
Conclusion
Regular cleaning of an RTO is crucial for effective air pollution control in industrial facilities. Mechanical, chemical, and steam cleaning methods can be employed to remove accumulated deposits and maintain optimal performance. By following best practices and adhering to a regular cleaning schedule, facility operators can ensure the longevity and efficiency of their RTOs. Remember to prioritize safety and document the cleaning process for future reference.
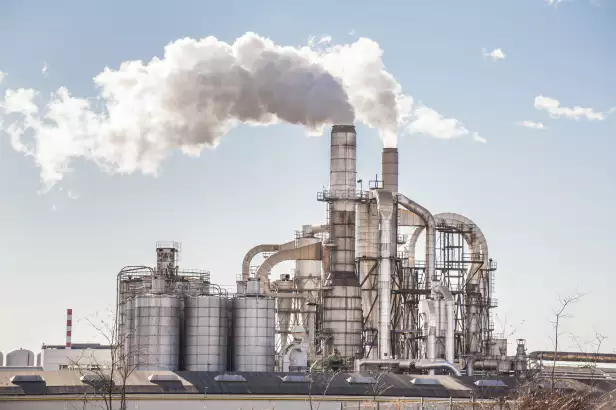

Company Introduction
Our company is a high-end equipment manufacturing enterprise specialized in comprehensive treatment of volatile organic compounds (VOCs) in exhaust gas and carbon reduction energy-saving technology. We have four core technologies: thermal energy, combustion, sealing, and automatic control. We possess capabilities in temperature field simulation, air flow field simulation modeling, ceramic heat storage material performance, molecular sieve adsorption material selection, and high-temperature incineration oxidation testing of VOCs organic compounds.
Team Advantages
We have RTO technology research and development center and waste gas carbon reduction engineering technology center in Xi’an, as well as a 30,000 square meter production base in Yangling. We are a leading manufacturer of RTO equipment and molecular sieve rotary wheel equipment in terms of production and sales volume globally. Our core technical team comes from the Aerospace Liquid Rocket Engine Research Institute (Aerospace Sixth Academy). With more than 360 employees, including over 60 R&D technology backbone members, we have 3 senior engineers at the researcher level, 6 senior engineers, and 47 thermodynamics doctors.
Core Products
Our core products include the rotary valve regenerative thermal oxidizer (RTO) and molecular sieve adsorption concentration rotary wheel. Combined with our expertise in environmental protection and thermal energy system engineering, we can provide customers with comprehensive solutions for industrial waste gas treatment, carbon reduction, and heat energy utilization under various operating conditions.
Certifications, Patents, and Honors
- Intellectual Property Management System Certification
- Quality Management System Certification
- Environmental Management System Certification
- Construction Industry Enterprise Qualification
- High-tech Enterprise
- Patents for Rotary Valve Regenerative Thermal Oxidizer
- Patents for Rotary Wheel Heat Storage Incineration Equipment
- Patents for Disc Molecular Sieve Rotary Wheel
How to Choose the Right RTO Equipment
- Determine the characteristics of the exhaust gas
- Understand local regulations and emission standards
- Evaluate energy efficiency
- Consider operation and maintenance
- Budget and cost analysis
- Select the appropriate RTO type
- Consider environmental and safety factors
- Performance testing and verification
It is important to understand the composition and properties of the exhaust gas to select the appropriate RTO equipment.
Compliance with local regulations and emission standards is crucial in selecting the suitable RTO equipment.
Assessing the energy efficiency of different RTO options helps in making an informed decision.
Considering the ease of operation and maintenance requirements ensures smooth operation of the RTO equipment.
Performing a budget and cost analysis helps in determining the most cost-effective RTO equipment.
Choosing the right RTO type based on the specific requirements of the application is essential.
Environmental and safety considerations play a significant role in selecting the suitable RTO equipment.
Conducting performance testing and verification ensures the effectiveness and reliability of the chosen RTO equipment.
RTO Air Pollution Control Service Process
- Preliminary consultation, on-site investigation, and needs analysis
- Solution design, simulation, and review
- Customized production, quality control, and factory testing
- On-site installation, commissioning, and training services
- Regular maintenance, technical support, and spare parts supply
We provide preliminary consultation, conduct on-site investigations, and perform needs analysis to understand the specific requirements of our clients.
We design customized solutions, perform simulation and modeling, and conduct thorough reviews to ensure the effectiveness and feasibility of the proposed solution.
We carry out customized production, stringent quality control measures, and comprehensive factory testing to deliver high-quality RTO equipment.
Our expert team handles on-site installation, commissioning, and provides training services to ensure the smooth operation of the RTO equipment.
We offer regular maintenance services, technical support, and a reliable supply of spare parts to keep the RTO equipment in optimal condition.
Our company offers a comprehensive one-stop solution for RTO air pollution control. With our professional team, we provide tailor-made RTO solutions for our clients.
Author: Miya