What are the environmental impact assessments for RTO in the coating industry?
介紹
In the coating industry, the use of Regenerative Thermal Oxidizers (RTOs) has become increasingly prevalent due to their ability to effectively control and minimize air pollution. RTOs are advanced air pollution control systems that utilize high temperatures to destroy volatile organic compounds (VOCs) and hazardous air pollutants (HAPs) emitted during the coating process. However, it is essential to conduct thorough environmental impact assessments to evaluate the potential effects of RTOs on the environment. This article aims to explore the various aspects and considerations involved in conducting environmental impact assessments for RTOs in the coating industry.
Assessment of Air Quality
– Measurement of VOC and HAP emissions
– Evaluation of air dispersion modeling
– Assessment of ambient air quality standards
– Monitoring of air pollutant concentrations near RTOs
– Analysis of the impact of RTOs on regional air quality
Energy Consumption and Efficiency
– Calculation of energy consumption by RTOs
– Assessment of energy efficiency improvements
– Comparison of energy consumption with alternative technologies
– Analysis of the potential for energy recovery from RTOs
– Evaluation of the overall environmental benefits of energy-efficient RTO systems
Waste Generation and Management
– Identification of waste streams from RTO operation
– Evaluation of waste treatment and disposal methods
– Assessment of the potential for waste reduction and recycling
– Analysis of the environmental impact of waste generated by RTOs
– Implementation of proper waste management practices
Health and Safety Considerations
– Identification of potential health risks associated with RTO emissions
– Assessment of worker exposure to VOCs and HAPs
– Analysis of the effectiveness of RTOs in reducing health hazards
– Evaluation of occupational health and safety measures
– Implementation of proper safety protocols and equipment
Regulatory Compliance
– Review of applicable environmental regulations and standards
– Assessment of RTO compliance with emission limits
– Analysis of permit requirements and reporting obligations
– Evaluation of the effectiveness of monitoring and control systems
– Compliance with local, national, and international environmental regulations
結論
In conclusion, conducting comprehensive environmental impact assessments for RTOs in the coating industry is crucial to ensure the effective control of air pollution and minimize environmental harm. By assessing air quality, energy consumption, waste generation, health and safety considerations, and regulatory compliance, the coating industry can make informed decisions regarding the implementation and operation of RTO systems. It is essential to prioritize sustainability and environmental protection to create a more sustainable and responsible coating industry.

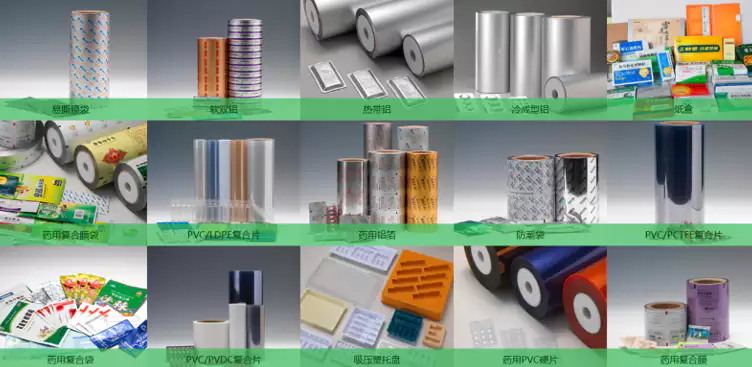
Environmental Impact Assessments for RTO in the Coating Industry
公司簡介:
Our company is a high-tech manufacturing enterprise specializing in the comprehensive treatment of volatile organic compounds (VOCs) exhaust gas and carbon reduction energy-saving technology. We have four core technologies: thermal energy, combustion, sealing, and self-control. We have the ability to simulate temperature fields and airflow fields, as well as the ability to test the properties of ceramic heat storage materials, select zeolite molecular sieve adsorption materials, and conduct high-temperature incineration and oxidation tests on VOCs organic substances.
團隊優勢:
We have an RTO technology research and development center and a waste gas carbon reduction engineering technology center in Xi’an, as well as a 30,000-square-meter production base in Yangling. We are a leading manufacturer of RTO equipment and zeolite molecular sieve rotary equipment worldwide. Our core technical team comes from the Aerospace Liquid Rocket Engine Research Institute (Aerospace Six Institute). We have more than 360 employees, including over 60 research and development technical backbones, including 3 senior engineers, 6 senior engineers, and 115 thermodynamic doctors.
核心產品:
Our core products are the Rotary Valve Regenerative Thermal Oxidizer (RTO) and the zeolite molecular sieve adsorption and concentration rotary wheel. Combined with our expertise in environmental protection and thermal energy system engineering technology, we can provide customers with comprehensive solutions for industrial waste gas treatment, carbon reduction, and energy utilization under various operating conditions.
Certifications and Qualifications:
- Management System Certification for Intellectual Property Rights
- 品質管理系統認證
- 環境管理系統認證
- 建築業企業資質
- 高新技術企業
- Patents for Rotary Valve Regenerative Thermal Oxidizer and Rotary Wheel Heat Storage Incineration Equipment
- Patent for Disc Zeolite Rotary Wheel
Choosing the Right RTO for the Coating Industry:
- 確定廢氣的特性
- 了解當地法規和排放標準
- 評估能源效率
- 考慮維
- 進行預算和成本分析
- 選擇適當的 RTO 類型
- 考慮環境和安全因素
- 執行效能測試和驗證
Regenerative Thermal Oxidizers Service Process:
- Initial consultation, on-site inspection, and needs analysis
- Solution design, simulation, and proposal review
- 客製化生產、品質控制和工廠測試
- 現場安裝、調試、培訓服務
- 定期維護、技術支援、備件供應
We are a one-stop solution for RTO and have a professional team to tailor RTO solutions for our customers.
Successful Cases of RTO for the Coating Industry:
Case 1: A company in Shanghai specializes in functional films such as diffusion films, prism films, micro-porous films, and solar films. The project consists of two phases with a 40,000 air volume RTO in the first phase and a 50,000 air volume RTO in the second phase.
Case 2: A technology company in Guangdong produces transfer paper, transfer film, electrolytic aluminum, polyester film, window film, protective film, etc. The total waste gas volume is 70,000 m3/h, and the equipment achieves standard emissions after completion.
Case 116: A company in Zhuhai produces wet lithium battery separators, and the system has been running smoothly without any faults.
作者:米婭