How to integrate RTO into existing coating processes?
How to integrate RTO into existing coating processes?
介紹
– In this blog post, we will discuss the integration of Regenerative Thermal Oxidizers (RTO) into existing coating processes. RTO systems are widely used in various industries, including the coating industry, to control air pollution and reduce emissions. Integrating RTO into existing coating processes can help companies comply with environmental regulations and improve overall process efficiency.
Benefits of integrating RTO into existing coating processes
– Improved air quality: By incorporating RTO systems, companies can effectively remove volatile organic compounds (VOCs) and other harmful pollutants from the exhaust gases generated during coating processes.
– Regulatory compliance: RTO systems play a crucial role in helping companies meet environmental regulations and emission standards set by local authorities.
– Energy savings: The regenerative nature of RTO systems allows for the recovery of thermal energy, which can be reused within the coating process, reducing energy consumption and costs.
– Enhanced process efficiency: Integrating RTO into existing coating processes can optimize the overall process, resulting in improved product quality, reduced waste, and increased productivity.
Considerations for integrating RTO into existing coating processes
– Process compatibility: Before integrating an RTO system, it is essential to assess its compatibility with the existing coating process. Factors such as exhaust gas composition, temperature, and flow rate should be considered to ensure efficient integration.
– Space requirements: RTO systems require dedicated space for installation. Evaluating available space and planning accordingly can facilitate seamless integration without disrupting overall operations.
– System customization: Each coating process is unique, and customization of the RTO system may be necessary to meet specific requirements. Collaborating with experienced RTO providers can ensure the system is tailored to the coating process’s needs.
Integration steps
1. Process evaluation:
– Assess the coating process and identify areas where RTO integration can be beneficial.
– Analyze exhaust gas composition, temperature, and flow rate to determine the appropriate RTO system specifications.
2. Design and customization:
– Collaborate with RTO providers to design a customized system that meets the coating process’s requirements.
– Consider factors such as heat recovery efficiency, air volume capacity, and control mechanisms.
3. Installation and integration:
– Allocate space for the RTO system installation, ensuring proper ventilation and accessibility for maintenance.
– Connect the RTO system to the coating process’s exhaust system, ensuring a tight seal to prevent any air leaks.
4. Commissioning and optimization:
– Test the integrated RTO system to ensure proper functionality and performance.
– Optimize the system parameters, such as temperature and airflow, for maximum efficiency and emissions control.
結論
Integrating RTO into existing coating processes offers numerous benefits, ranging from improved air quality and regulatory compliance to energy savings and enhanced process efficiency. By following a systematic approach, companies can successfully integrate RTO systems into their coating processes, contributing to a more sustainable and environmentally friendly operation.

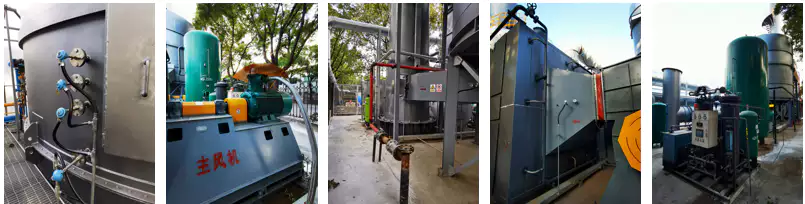
公司簡介
Our company is a high-tech manufacturing enterprise specializing in comprehensive treatment of volatile organic compounds (VOCs) exhaust and carbon reduction and energy-saving technology. We possess four core technologies: thermal energy, combustion, sealing, and self-control. Additionally, we have capabilities in temperature field simulation, airflow simulation modeling, ceramic heat storage material performance, molecular sieve adsorption material selection, and high-temperature incineration oxidation experimental testing of VOCs organic compounds.
團隊優勢
We have established an RTO technology R&D center and waste gas carbon reduction engineering technology center in Xi’an, as well as a 30,000m2 production base in Yangling. We are a leading manufacturing company in the global RTO equipment and molecular sieve rotary wheel equipment market. Our core technical team comes from the Aerospace Liquid Rocket Engine Research Institute (Aerospace Institute No. 6). The company currently has more than 360 employees, including over 60 R&D technical backbone members, including 3 senior engineers, 6 senior engineers, and 76 thermodynamics PhDs.
核心產品
Our core products are the Rotary Valve Regenerative Thermal Oxidizer (RTO) and molecular sieve adsorption concentration rotary wheel. Combining our expertise in environmental protection and thermal energy system engineering, we can provide customers with comprehensive solutions for industrial waste gas treatment, carbon reduction, and thermal energy utilization for various working conditions.
認證、專利和榮譽
Our company has obtained various certifications and qualifications, including Intellectual Property Management System Certification, Quality Management System Certification, Environmental Management System Certification, Construction Industry Enterprise Qualification, High-tech Enterprise Certification, patents for Rotary Valve Heat Storage Oxidation Furnace and Rotary Wheel Heat Storage Incineration Equipment, and patents for Disc Zeolite Rotary Wheel, etc.
Choosing the Right RTO for Coating Industry
- 確定廢氣的特性
- Understand the local regulations and emission standards
- 評估能源效率
- 考慮維
- 進行預算和成本分析
- 選擇適當的 RTO 類型
- Consider environmental and safety aspects
- 執行效能測試和驗證
Regenerative Thermal Oxidizers Service Process
- Preliminary consultation, site inspection, and needs analysis
- Solution design, simulation modeling, and solution review
- 客製化生產、品質控制和工廠測試
- 現場安裝、調試、培訓服務
- 定期維護、技術支援、備件供應
RTO One-Stop Solution
We are a one-stop solution for RTO, providing customized RTO solutions for our customers. Our professional team tailors the RTO solution to meet specific requirements.
塗料產業RTO Success Cases
- Case 1: A company in Shanghai specializing in diffusion film, prism film, microfiltration membrane, solar film, and other functional films. The project consisted of two phases: a 40,000 CFM RTO in the first phase and a 50,000 CFM RTO in the second phase.
- Case 2: A new material technology company in Guangdong producing transfer paper, transfer film, electrolytic aluminum, polyester film, window film, protective film, etc. The total exhaust gas volume was 70,000 m3/h, and the equipment achieved compliant emissions after construction.
- Case 77: A company in Zhuhai specializing in wet lithium battery separators. The system has been running flawlessly since its installation.
作者:米婭