What are the key features of RTO for coating industry?
Úvod
The coating industry faces numerous challenges when it comes to controlling air pollution and reducing emissions. Regenerative Thermal Oxidizers (RTOs) have emerged as a key solution to address these concerns. RTOs offer unique features and advantages that make them well-suited for the coating industry. In this article, we will explore the key features of RTOs and how they benefit the coating industry.
High Thermal Efficiency
– RTOs are known for their high thermal efficiency, which allows them to effectively destroy volatile organic compounds (VOCs) emitted during the coating process.
– The system uses a regenerative heat exchanger to recover and reuse the heat generated during the oxidation process, leading to significant energy savings.
– This high thermal efficiency not only reduces operational costs but also minimizes the environmental impact of the coating industry.
Low Operating Costs
– RTOs are designed to minimize operating costs for the coating industry. The regenerative heat exchanger allows for energy recovery, reducing the need for additional fuel or electricity.
– The system is automated, requiring minimal manual intervention and reducing labor costs.
– RTOs also have low maintenance requirements, resulting in lower maintenance costs over the system’s lifespan.
Effective VOC Destruction
– One of the key features of RTOs is their ability to effectively destroy VOCs emitted during the coating process.
– The high temperature and residence time within the oxidizer chamber ensure the complete oxidation of VOCs into carbon dioxide and water vapor, eliminating harmful emissions.
– This efficient VOC destruction ensures compliance with environmental regulations and helps the coating industry maintain a clean and sustainable operation.
Flexible Operation
– RTOs offer flexibility in operation, allowing the coating industry to adapt to varying process conditions.
– The system can handle a wide range of flow rates and concentrations, accommodating different coating processes and production levels.
– RTOs can also handle variations in VOC concentrations, providing reliable performance even during peak emissions.
Reliable and Durable
– RTOs are known for their reliability and durability, making them a trusted solution for the coating industry.
– The system is designed with robust materials and components, capable of withstanding harsh operating conditions and extended operational hours.
– With proper maintenance and care, RTOs can provide long-term performance, ensuring uninterrupted operation for the coating industry.
Záver
RTOs offer a range of key features that make them an ideal choice for the coating industry. Their high thermal efficiency, low operating costs, effective VOC destruction, flexible operation, and reliability make them a valuable asset in controlling air pollution and reducing emissions. By adopting RTOs, the coating industry can achieve regulatory compliance, improve sustainability, and maintain a competitive edge in the market.

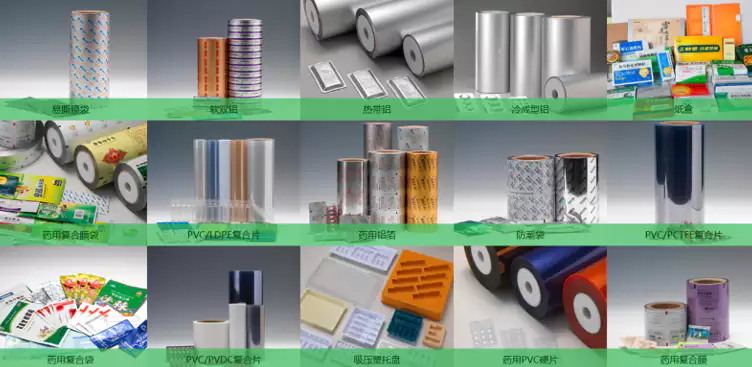
Key Features of RTO for Coating Industry
Our company is a high-tech enterprise that focuses on the comprehensive treatment of volatile organic compound (VOC) waste gas and carbon reduction and energy-saving technology. We have four core technologies in thermal energy, combustion, sealing, and self-control, and possess the ability to simulate temperature field and air flow field, model and calculate properties of ceramic heat storage materials, select molecular sieve adsorption materials, and test characteristics of high-temperature incineration and oxidation of VOC organic substances.
Our team has many advantages. We have an RTO technology research and development center and waste gas carbon reduction engineering technology center in Xi’an, and a 30,000 square meter production base in Yangling. We are a leading manufacturer of RTO equipment and molecular sieve rotary equipment in the world. Our core technology team comes from the research institute of liquid rocket engines of China Aerospace Science and Technology Corporation (CASC), and we currently have more than 360 employees, including more than 60 R&D technical backbones, 3 research fellows, 6 senior engineers, and 75 thermodynamics PhDs.
Our core products are the rotary valve heat storage oxidation incinerator (RTO) and molecular sieve adsorption concentration rotary equipment. Combining our own environmental protection and thermal energy system engineering technology expertise, we can provide customers with comprehensive solutions for industrial waste gas treatment and carbon reduction and energy utilization under various working conditions.
Our company has many certifications, such as the knowledge property management system certification, quality management system certification, environmental management system certification, construction industry enterprise qualification, high-tech enterprise, rotary valve heat storage oxidation furnace rotary valve patent, rotary wing heat storage incineration device patent, and disc-shaped molecular sieve rotary patent, among others.
To choose the appropriate RTO for coating industry, there are several factors to consider:
- Determine the waste gas characteristics.
- Understand the local regulations and set emission standards.
- Evaluate energy efficiency.
- Consider operation and maintenance.
- Conduct budget and cost analysis.
- Choose the appropriate type of RTO.
- Consider environmental and safety factors.
- Perform performance testing and verification.
Our regenerative thermal oxidizers service process includes preliminary consultation, on-site inspections, demand analysis, solution design, simulation and modeling, solution review, customized production, quality control, factory testing, on-site installation, commissioning operation, training services, regular maintenance, technical support, and spare parts supply.
We are a one-stop solution for RTOs and have a professional team to customize RTO solutions for our customers. Here are some successful cases of our RTO for coating industry:
- Case 1: A Shanghai enterprise’s main products are functional films such as diffusion films, prism films, micro-permeable films, and solar films. The project is divided into two phases. The first phase has a 40,000 air volume RTO, and the second phase has a 50,000 air volume RTO.
- Case 2: A Guangdong new materials technology company’s main products include transfer paper, transfer film, electro-aluminum, polyester film, window film, protective film, etc. The total amount of waste gas is 70,000m3/h, and the equipment will achieve standard emission after completion.
- Case 76: Zhuhai new materials technology company’s main product is wet lithium battery diaphragm, and the system has been running without failure since self-operation.
Autor: Miya