What are the best practices for RTO in the printing industry?
Introducción
In the printing industry, implementing effective practices for Regenerative Thermal Oxidizers (RTO) is crucial for optimizing performance and reducing environmental impact. RTOs are widely used in the printing industry to control emissions and ensure compliance with regulatory standards. This article will explore the best practices for RTOs in the printing industry, focusing on various aspects and angles to provide a comprehensive understanding of their usage and benefits.
Benefits of Implementing RTOs
– Improved Air Quality: RTOs help in eliminating pollutants and volatile organic compounds (VOCs) released during the printing process, leading to improved air quality.
– Energy Efficiency: By utilizing the captured heat during the oxidation process, RTOs can save energy and reduce operational costs.
– Compliance with Regulations: Implementing RTOs ensures compliance with stringent environmental regulations and avoids potential penalties or legal issues.
– Reduction in Odors: RTOs aid in minimizing odors generated by the printing process, creating a better working environment for employees.
Design Considerations for RTOs
– Size and Capacity: Properly sizing the RTO system based on the printing facility’s emissions is essential for optimal performance.
– Heat Recovery: Incorporating effective heat recovery mechanisms, such as ceramic media beds, can significantly increase energy efficiency.
– Temperature Control: Maintaining precise temperature control within the RTO is crucial for achieving efficient oxidation of pollutants.
– Monitoring and Control Systems: Implementing advanced monitoring and control systems allows for real-time data analysis and adjustment, ensuring optimal RTO performance.
Installation and Maintenance
– Professional Installation: It is crucial to engage experienced professionals for the installation of RTO systems to ensure correct setup and functionality.
– Regular Inspections: Scheduled inspections and maintenance routines help identify and address any potential issues promptly, ensuring continuous operation.
– Cleaning and Replacement: Regular cleaning and replacement of heat exchange media and filters prevent blockages and ensure efficient operation.
– Performance Monitoring: Implementing a comprehensive performance monitoring program helps detect any deviations or inefficiencies, allowing for timely corrective actions.
Case Studies
– Company A: By implementing an RTO system, Company A reduced VOC emissions by 70% while achieving substantial energy savings.
– Company B: The installation of an RTO system at Company B’s printing facility resolved odor issues and improved employee satisfaction, leading to increased productivity.
Conclusión
Implementing the best practices for RTOs in the printing industry brings numerous benefits, including improved air quality, energy efficiency, compliance with regulations, and odor reduction. By considering design elements, proper installation, regular maintenance, and performance monitoring, printing companies can maximize the effectiveness of their RTO systems. Embracing these practices not only enhances environmental sustainability but also contributes to a more efficient and profitable printing operation.
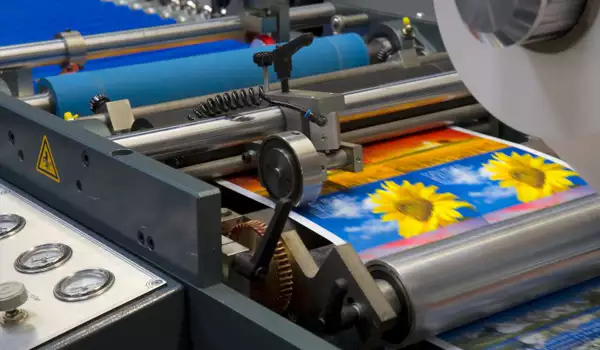

Presentación de la empresa
We are a high-tech manufacturing enterprise specializing in comprehensive treatment of volatile organic compounds (VOCs) exhaust gas and carbon reduction and energy-saving technologies. Our core technologies include thermal energy, combustion, sealing, and control. We have the capabilities for temperature field simulation, air flow field simulation modeling, ceramic heat storage material performance, molecular sieve adsorbent material selection, and VOCs high-temperature incineration and oxidation experimental testing.
Team Advantage
We have established RTO technology research and development center and exhaust gas carbon reduction engineering technology center in Xi’an, as well as a 30,000 square meters production base in Yangling. We are a leading manufacturer of RTO equipment and molecular sieve rotary wheel equipment in the global market. Our core technical team comes from the Liquid Rocket Engine Research Institute of the China Aerospace Science and Technology Corporation (CAST), and we currently have more than 360 employees, including over 60 research and development technical backbones. Among them, there are 3 senior engineers with the title of researcher, 6 senior engineers, and 47 PhDs in thermodynamics.
Core Products
Our core products include the Rotary Valve Regenerative Thermal Oxidizer (RTO) and molecular sieve adsorption concentration rotary wheel. Combined with our expertise in environmental protection and thermal energy system engineering, we can provide customers with comprehensive solutions for industrial exhaust gas treatment and carbon reduction through thermal energy utilization under various operating conditions.
Our company has obtained the following certifications, qualifications, patents, and honors: Intellectual Property Management System Certification, Quality Management System Certification, Environmental Management System Certification, Construction Industry Enterprise Qualification, High-tech Enterprise, Rotary Heat Storage Oxidation Furnace Rotary Valve Patent, Rotary Heat Storage Incineration Equipment Patent, Disc-Type Zeolite Rotary Wheel Patent, etc.
How to Choose the Right RTO Equipment
- Determine exhaust gas characteristics.
- Comprenda las regulaciones locales y los estándares de emisiones.
- Evaluar la eficiencia energética.
- Considere la operación y el mantenimiento.
- Análisis de presupuesto y costos.
- Select the appropriate type of RTO.
- Considere los factores ambientales y de seguridad.
- Performance testing and verification.
When choosing the right RTO equipment, it is important to:
- Explain the exhaust gas characteristics and how they impact the selection process.
- Discuss the local regulations and emission standards that need to be met.
- Explain how energy efficiency is evaluated and why it is important.
- Highlight the importance of considering operation and maintenance factors for long-term effectiveness.
- Discuss the budget and cost analysis considerations for selecting the most suitable equipment.
- Explain the different types of RTO and their respective advantages.
- Discuss the environmental and safety considerations during the selection process.
- Explain the importance of performance testing and verification to ensure the chosen equipment meets the requirements.
Nuestro proceso de servicio
- Preliminary consultation, on-site inspection, and demand analysis.
- Solution design, simulation modeling, and solution review.
- Customized production, quality control, and factory testing.
- On-site installation, commissioning, and training services.
- Regular maintenance, technical support, and spare parts supply.
We provide a one-stop solution and have a professional team that tailors RTO solutions to meet the specific needs of our customers.
Autor: Miya