How does RTO work in the printing industry?
Introducción
In the printing industry, the use of Regenerative Thermal Oxidizers (RTOs) has become increasingly common to control air pollution and minimize harmful emissions. RTOs are advanced pollution control systems that utilize high temperatures to eliminate volatile organic compounds (VOCs) and other pollutants from the exhaust gases generated during the printing process. This article aims to explore the various aspects of how RTOs work in the printing industry and their significance in maintaining environmental sustainability.
Understanding RTOs
– RTOs are designed to treat the exhaust gases by oxidizing the VOCs into harmless byproducts through high-temperature combustion.
– The system consists of a combustion chamber, ceramic heat exchange beds, and a control unit to ensure efficient operation.
– The ceramic heat exchange beds alternate between two modes: the “clean air” mode and the “dirty air” mode, allowing for continuous treatment of the exhaust gases.
– During the “clean air” mode, the VOC-laden air passes through one heat exchange bed while the other bed is heated, storing thermal energy for the next cycle.
– In the “dirty air” mode, the direction of the airflow is reversed, allowing the heated bed to release energy and raise the temperature of the incoming VOC-laden air for oxidation.
– The RTO system operates cyclically, efficiently utilizing heat and minimizing energy consumption.
The Working Principle of RTOs in the Printing Industry
– Preheating Stage:
– The exhaust gases from the printing process enter the RTO system through the inlet duct.
– Before entering the combustion chamber, the gases pass through a preheating section where the heat exchange beds heat them to the required oxidation temperature.
– This preheating process optimizes the system’s efficiency by utilizing the heat energy from the outgoing gases.
The Oxidation Process
– Combustion Chamber:
– Once the exhaust gases reach the combustion chamber, the temperature is increased to the combustion level.
– In this chamber, the VOCs present in the gases react with oxygen, resulting in their complete oxidation.
– The RTO system ensures a high residence time within the combustion chamber to ensure thorough oxidation.
Heat Recovery
– Ceramic Heat Exchange Beds:
– After the oxidation process, the gases pass through the ceramic heat exchange beds.
– In the “clean air” mode, the beds absorb the heat from the outgoing gases, transferring it to the incoming VOC-laden air.
– This heat recovery process significantly reduces the energy requirements of the system.
Environmental Benefits of RTOs in the Printing Industry
– Reduction of Harmful Emissions:
– RTOs effectively eliminate VOCs and other pollutants, minimizing the environmental impact of the printing industry.
– The combustion process within the RTO system converts VOCs into carbon dioxide and water vapor, which are harmless byproducts.
– Compliance with Regulations:
– By implementing RTOs, printing companies can ensure compliance with stringent air quality regulations and avoid potential penalties.
– Energy Efficiency:
– RTOs are designed to recover and reuse thermal energy, reducing the overall energy consumption of the printing process.
Conclusión
In conclusion, RTOs play a crucial role in the printing industry by efficiently controlling air pollution and reducing harmful emissions. These advanced systems utilize high temperatures, combustion chambers, and ceramic heat exchange beds to oxidize VOCs and minimize the environmental impact of the printing process. By implementing RTOs, printing companies can achieve environmental sustainability, comply with regulations, and enhance their overall operational efficiency.
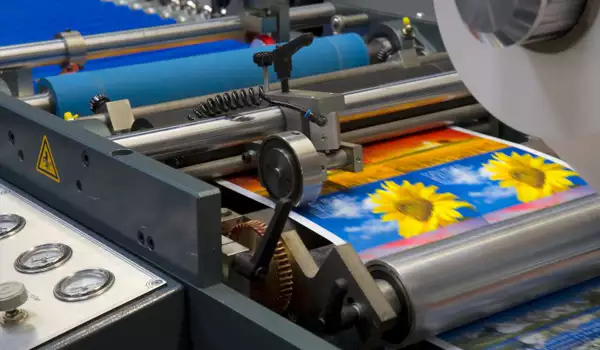

How RTO Works in the Printing Industry
Our company specializes in comprehensive treatment of volatile organic compounds (VOCs) and carbon reduction energy-saving technology. We have four core technologies: thermal, combustion, sealing, and self-control. Our team has the ability to simulate temperature and air flow fields, compare and select ceramic heat storage materials and zeolite molecular sieve adsorbents, and test high-temperature incineration and oxidation properties of VOCs. We have a RTO technology research and development center and a waste gas carbon reduction engineering technology center in Xi’an, and a 30,000 square meter production base in Yangling. Our core technology team comes from the Aerospace Liquid Rocket Engine Research Institute, and we have over 360 employees, including over 60 R&D technology backbones.
Our core products are rotary valve regenerative thermal oxidation furnaces (RTO) and zeolite molecular sieve adsorption and concentration rotors. Combined with our own environmental protection and thermal energy system engineering technology expertise, we can provide customers with comprehensive solutions for industrial waste gas treatment and carbon reduction and utilization of thermal energy under various working conditions.
Certifications, Patents, and Honors
- Intellectual Property Management System Certification
- Quality management system certification
- Environmental management system certification
- Construction industry enterprise qualification
- High-tech enterprise
- Patents for rotary valve regenerative thermal oxidation furnace and rotor-type heat storage incineration equipment
- Patent for disc-type zeolite rotor
How to Choose the Right RTO Equipment
- Determine the characteristics of the waste gas
- Understand the emission standards set by local regulations
- Evaluate energy efficiency
- Consider operation and maintenance
- Budget and cost analysis
- Choose the appropriate type of RTO
- Consider environmental and safety factors
- Performance testing and validation
When choosing the right RTO equipment, it is important to consider the characteristics of the waste gas, such as the composition and concentration of the VOCs. It is also important to understand the local regulations and emission standards that must be met. Evaluating energy efficiency can help you choose an RTO that will be cost-effective in the long run. Considering operation and maintenance, as well as budget and cost analysis, can help you make an informed decision. Choosing the appropriate type of RTO will depend on your specific needs, and environmental and safety factors should also be taken into account. Finally, performance testing and validation can ensure that the equipment is working as it should.
Nuestro proceso de servicio
- Preliminary consultation, on-site investigation, and needs analysis
- Scheme design, simulation and evaluation, and scheme review
- Customized production, quality control, and factory testing
- On-site installation, commissioning, and training services
- Regular maintenance, technical support, and spare parts supply
At our company, we provide a one-stop solution for our clients with a team of professionals who can customize RTO solutions to their specific needs. Our service process includes preliminary consultation, on-site investigation, and needs analysis to help us understand the unique requirements of each client. We then use our expertise to design the best solution, which includes simulation and evaluation, as well as scheme review. We then customize production, conduct quality control, and perform factory testing to ensure that the equipment meets our high standards. We also offer on-site installation, commissioning, and training services to help our clients get the most out of their RTO equipment. Finally, we provide regular maintenance, technical support, and spare parts supply to ensure that the equipment works as it should for years to come.
Autor: Miya