RTO air pollution control system design considerations
Introduction
In recent years, air pollution has become a pressing issue that requires effective solutions. One such solution is the use of Regenerative Thermal Oxidizers (RTOs) for air pollution control. RTOs are widely employed in various industries due to their high efficiency in removing volatile organic compounds (VOCs) and hazardous air pollutants (HAPs). However, the design of an RTO kontrola znečištění ovzduší system requires careful consideration of several factors to ensure optimal performance and compliance with environmental regulations.
System Capacity
– The first consideration in RTO design is determining the system capacity. This involves estimating the amount of air to be treated per hour and selecting the appropriate size of the RTO unit. Factors such as process exhaust flow rate, pollutant concentration, and temperature must be taken into account to ensure the system can handle the expected load.
– Proper sizing of the RTO is crucial to avoid underutilization or overloading, both of which can lead to inefficiencies. An undersized RTO may not effectively treat the exhaust gases, while an oversized one may consume excessive energy.
Heat Recovery Efficiency
– Heat recovery efficiency is another important aspect of RTO design. RTOs utilize a ceramic heat exchange media to transfer heat from the outgoing exhaust gases to the incoming process air. Maximizing heat recovery allows for energy conservation and cost reduction.
– Factors influencing heat recovery efficiency include the choice of heat exchange media, the design of the heat exchange chambers, and the control of air flow rates. Proper insulation and sealing of the system also contribute to minimizing heat losses.
Pressure Drop
– Pressure drop is a critical consideration in RTO design as it affects the overall system performance. The pressure drop across the RTO unit should be optimized to ensure efficient operation without compromising the airflow rate and treatment efficiency.
– Factors influencing pressure drop include the design of the ceramic heat exchange media, the configuration of the flue gas ductwork, and the selection of control valves. Proper sizing and layout of these components are essential in minimizing pressure drop and avoiding unnecessary energy consumption.
Control System
– An effective control system is vital for the proper operation of an RTO air pollution control system. The control system monitors and adjusts various parameters such as temperature, air flow, and pollutant concentration to maintain optimal performance.
– Advanced control algorithms, sensors, and data acquisition systems are commonly used in modern RTO designs. The control system should be capable of providing real-time feedback, ensuring stable and efficient operation of the RTO unit.
Maintenance and Inspection
– Regular maintenance and inspection are crucial for the longevity and optimal performance of an RTO air pollution control system. Proper maintenance practices should be implemented to prevent malfunctions and ensure compliance with environmental regulations.
– Routine inspections, cleaning of heat exchange media, and calibration of control instruments are essential tasks in maintaining an RTO system. Additionally, any necessary repairs or component replacements should be promptly addressed to avoid system downtime and potential environmental non-compliance.
Conclusion
In conclusion, the design of an RTO air pollution control system requires careful consideration of various factors. System capacity, heat recovery efficiency, pressure drop, control system, and maintenance are all critical aspects that must be addressed to ensure the system’s optimal performance, energy efficiency, and compliance with environmental regulations. By adhering to these design considerations, industries can effectively mitigate air pollution and contribute to a cleaner and healthier environment.
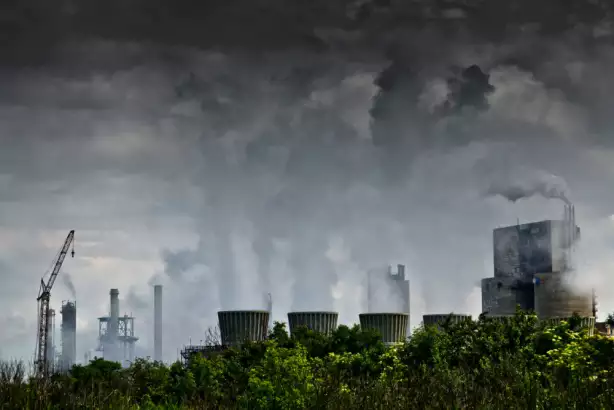

Introduction to Our Company
Our company is a high-end equipment manufacturing high-tech enterprise specializing in comprehensive treatment of volatile organic compounds (VOCs) waste gas and carbon reduction and energy-saving technology. We have four core technologies in thermal energy, combustion, sealing, and self-control. We also have the ability to simulate temperature fields and air flow fields, model calculations, compare ceramic heat storage materials and zeolite molecular sieve adsorption materials, and conduct VOCs organic high-temperature incineration and oxidation experiments. We have an RTO technology R&D center and waste gas carbon reduction engineering technology center in Xi’an, and a 30,000 square meter production base in Yangling. Our core technology team comes from the Aerospace Liquid Rocket Engine Research Institute (Aerospace Sixth Institute). We have more than 360 employees, including more than 60 R&D technical backbones, including 3 senior engineers at the researcher level, 6 senior engineers, and 47 thermodynamics doctors.
Our core products include the rotary valve-type heat-storage oxidation incinerator (RTO) and the zeolite molecular sieve adsorption and concentration rotor. Combined with our own environmental protection and thermal energy system engineering expertise, we can provide customers with industrial waste gas comprehensive treatment and thermal energy utilization carbon reduction integrated solutions for various working conditions.
Certifications, Patents, and Honors
Our company has obtained the following certifications and qualifications: knowledge intellectual property management system certification, quality management system certification, environmental management system certification, construction industry enterprise qualification, high-tech enterprise, rotary heat storage oxidation furnace turning valve patent, rotor heat storage incineration equipment patent, and plate zeolite turning wheel patent, etc.
Choosing the Right RTO Equipment
When choosing the right RTO equipment, it is important to consider the following factors:
- Identifying the characteristics of the waste gas
- Understanding the local regulations and emission standards
- Evaluating energy efficiency
- Considering operation and maintenance
- Analýza rozpočtu a nákladů
- Choosing the appropriate type of RTO
- Considering environmental and safety factors
- Performance testing and validation
Understanding these factors will help ensure that you select the right RTO equipment that meets your needs.
RTO Air Pollution Control Service Process
Our RTO air pollution control service process includes:
- Initial consultation, on-site investigation, and needs analysis
- Plan design, simulation modeling, and plan review
- Zakázková výroba, kontrola kvality a tovární testování
- Instalace, uvedení do provozu a školení na místě
- Pravidelná údržba, technická podpora a dodávky náhradních dílů
Our professional team can provide customers with customized RTO solutions to meet their specific needs, making us your one-stop solution for RTO air pollution control.
Autor: Miya