VOC Abatement in Coating Industry
Введение
Volatile organic compounds (VOCs) are chemicals that easily vaporize at room temperature, posing significant environmental and health risks. In the coating industry, VOC emissions are a major concern due to their contribution to air pollution and the potential health hazards they pose to workers. This article will delve into various aspects of VOC abatement in the coating industry, exploring different strategies and technologies employed to mitigate VOC emissions.
Regulatory Requirements
– Stringent environmental regulations have been implemented globally to control VOC emissions in the coating industry.
– Compliance with these regulations often necessitates the adoption of VOC abatement measures.
VOC Abatement Technologies
– Thermal Oxidizers:
– Regenerative Thermal Oxidizers (RTOs):
– RTOs are widely used in the coating industry to reduce VOC emissions.
– The operating principle involves the use of a regenerative heat exchanger to preheat the incoming process air, reducing fuel consumption.
– RTOs achieve high VOC destruction efficiencies, typically above 95%.
– Catalytic Oxidizers:
– Catalytic oxidizers use a catalyst to lower the temperature required for VOC oxidation, resulting in energy savings.
– They are effective for VOC abatement in low-temperature coating processes.
– The catalyst provides a surface for the VOC oxidation reaction to occur, increasing the reaction rate.
– Adsorption Systems:
– Activated Carbon Adsorption:
– Activated carbon is commonly used for VOC removal by adsorption.
– Its high surface area and porosity allow for effective VOC capture.
– The adsorption process involves the retention of VOC molecules on the carbon surface.
– Zeolite Adsorption:
– Zeolite materials have been found to be effective in VOC removal due to their unique molecular sieve properties.
– They selectively adsorb VOC molecules based on their size, shape, and polarity.
– Zeolite adsorption systems are known for their high capacity and regenerability.
Best Practices in VOC Abatement
– Process Optimization:
– Implementing efficient coating techniques, such as powder coating or high-solids coatings, can reduce VOC emissions.
– Optimizing the curing process through heat recovery systems or infrared technology can minimize VOC release.
– Recycling and Recovery:
– VOC recovery systems can capture and recycle solvent-rich air streams, reducing waste and emissions.
– Distillation and condensation processes are commonly used to recover VOCs from exhaust streams.
– Employee Training and Awareness:
– Proper training and awareness programs for employees can help minimize VOC emissions.
– Educating workers on the importance of VOC abatement and the proper handling of coating materials is crucial.
Заключение
VOC abatement in the coating industry is vital for environmental protection and worker safety. Regulatory requirements and the adoption of efficient technologies have driven significant advancements in VOC reduction. By implementing appropriate VOC abatement strategies, such as thermal oxidizers and adsorption systems, along with process optimization and employee training, the coating industry can achieve substantial emissions reductions while maintaining high-quality production.

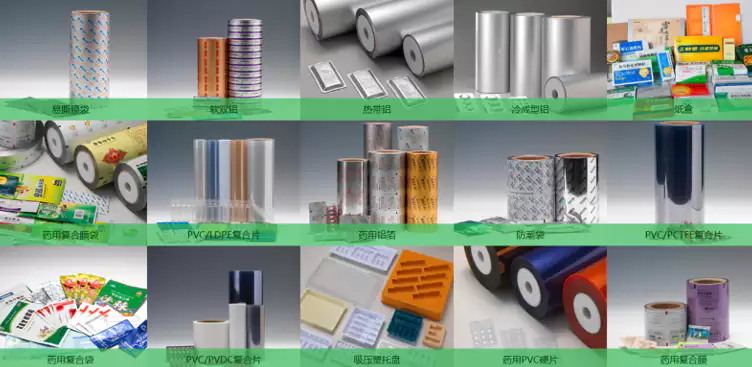
Введение в компанию
We are a high-tech enterprise that focuses on comprehensive treatment of volatile organic compound (VOC) waste gas and carbon reduction and energy saving technology. Our company has four core technologies: thermal energy, combustion, sealing, and self-control. We have the ability to simulate temperature fields and air flow fields, as well as to model ceramic heat storage material properties, select zeolite molecular sieve adsorption materials, and test the characteristics of VOC organic high temperature incineration and oxidation. We have an RTO technology R&D center and waste gas carbon reduction engineering technology center in Xi’an, and a production base of 30,000 square meters in Yangling. Our core technology team comes from the Liquid Rocket Engine Research Institute of the China Academy of Aerospace (CALT). We have more than 360 employees, including more than 60 R&D technology backbones, three senior engineer-level researchers, six senior engineers, and 25 thermodynamics PhDs. Our core products are the rotary valve type heat storage oxidation incinerator (RTO) and the zeolite molecular sieve adsorption and concentration rotor. Combined with our own environmental protection and thermal energy system engineering technical expertise, we can provide customers with comprehensive solutions for industrial waste gas treatment and carbon reduction with thermal energy utilization.
Certifications, Patents and Honors
Our company has obtained certifications and qualifications including knowledge property management system certification, quality management system certification, environmental management system certification, construction industry enterprise qualification, high-tech enterprise, rotary valve type heat storage oxidation furnace turning valve patent, rotary wing type heat storage incineration equipment patent, and disc type zeolite rotor patent. Our company has also won numerous honors. See the image below for the certification of our products:
How to Choose the Right RTO for Coating Industry
- Определить характеристики отходящих газов
- Learn about local regulations and established emission standards
- Оценить энергоэффективность
- Рассмотрим эксплуатацию и техническое обслуживание
- Анализ бюджета и затрат
- Выберите правильный тип RTO
- Учитывайте факторы окружающей среды и безопасности
- Тестирование и проверка производительности
Understand the composition and concentration of VOCs, as well as the temperature, humidity, and pressure of the waste gas.
Understand the local environmental protection standards and the requirements for waste gas emissions, as well as the relevant laws and regulations of the country or region.
Understand the energy consumption and heat recovery efficiency of the equipment, and evaluate the energy saving effect and economic benefits.
Understand the operation and maintenance requirements of the equipment, as well as the training and support provided by the manufacturer.
Understand the total cost of equipment procurement, installation, operation, and maintenance, and evaluate the economic benefits and payback period of the investment.
Choose the RTO that best suits the characteristics of the waste gas, taking into account factors such as temperature, concentration and flow rate, etc.
Understand the environmental and safety factors of the equipment, such as noise, vibration, exhaust emissions and fire prevention and explosion protection measures.
Before purchasing equipment, verify the performance and effectiveness of the RTO through on-site testing, simulation testing, or other means.
Service Process of Regenerative Thermal Oxidizers
Our service process includes:
- Initial consultation, on-site inspection, and demand analysis
- Program design, simulation and review
- Custom production, quality control, and factory testing
- Услуги по установке, вводу в эксплуатацию и обучению на месте
- Регулярное обслуживание, техническая поддержка и поставка запасных частей
Understand the customer’s production process, waste gas composition and concentration, emission standards, energy consumption and other relevant information, and analyze the customer’s actual needs.
Provide personalized RTO solutions based on customer needs, simulate and optimize the process, and provide a detailed review report.
Manufacture RTO equipment according to customer needs, conduct strict quality control during the production process, and conduct factory testing to ensure product quality.
Provide on-site installation and commissioning services, and provide training on equipment operation and maintenance for customer personnel.
Provide regular maintenance and technical support services, and provide customers with spare parts supply services.
We provide one-stop RTO solutions with a professional team to tailor RTO solutions for customers. Here are some successful RTO coating industry cases:
- Case 1: A Shanghai-based enterprise’s main products are functional films such as diffusion films, prism films, micro-porous films, and sun films. The project is divided into two phases, with a 40,000 air volume RTO in the first phase and a 50,000 air volume RTO in the second phase.
- Case 2: Guangdong-based new material technology company’s main products include transfer paper, transfer film, electrolytic aluminum, polyester film, window film, protective film, etc., with a total waste gas volume of 70,000 m3/h. Equipment construction has achieved standard emissions.
- Case 3: Zhuhai-based new material technology company’s main product is wet lithium-ion battery separator, and the system has been running without failure since it was put into operation.
Автор: Мия