RTO vs. other oxidation technologies for coatings
pengenalan
– Regenerative Thermal Oxidizers (RTO) and other oxidation technologies play a crucial role in the coatings industry. This article will explore the advantages and disadvantages of RTO compared to other oxidation technologies for coatings.
Understanding RTO
– RTO is a highly effective and energy-efficient oxidation technology used in the coatings industry. It utilizes a regenerative process to remove volatile organic compounds (VOCs) from exhaust gases generated during coating operations.
– The regenerative process involves the cyclic heating and cooling of ceramic beds, allowing for the efficient destruction of VOCs and the recovery of heat energy.
– RTOs are known for their high destruction efficiency, typically exceeding 98%, making them a preferred choice for many coating manufacturers.
Advantages of RTO
– Energy Efficiency:
– RTOs offer exceptional energy efficiency due to their regenerative design. The heat energy recovered during the oxidation process can be utilized to preheat incoming exhaust gases, reducing the overall energy consumption.
– This energy-saving feature not only reduces operational costs but also contributes to a more sustainable and environmentally friendly coating process.
– High Destruction Efficiency:
– As mentioned earlier, RTOs achieve destruction efficiencies of over 98%. This high efficiency ensures the effective removal of VOCs, preventing their release into the environment and helping coating manufacturers comply with stringent air quality regulations.
– Versatility:
– RTOs can handle a wide range of coating applications, including solvent-based and water-based coatings. Their versatility makes them suitable for various industries, from automotive to aerospace.
Drawbacks of RTO
– Capital Investment:
– Implementing an RTO system can involve significant upfront costs. The need for specialized equipment, such as ceramic beds and heat recovery systems, can make the initial investment higher compared to other oxidation technologies.
– Space Requirements:
– RTOs require sufficient space for installation, especially when considering the size of the ceramic beds and other components. Coating manufacturers with limited space may find it challenging to accommodate an RTO system.
– Maintenance and Operational Complexity:
– RTOs require regular maintenance to ensure optimal performance. The complexity of the regenerative process and the need for periodic cleaning and inspection can add to the operational challenges.
Kesimpulan
– In conclusion, RTOs offer numerous advantages in terms of energy efficiency, destruction efficiency, and versatility. However, they also come with drawbacks such as capital investment, space requirements, and maintenance complexity. Coating manufacturers should carefully consider their specific requirements and evaluate the pros and cons before choosing between RTO and other oxidation technologies for their coatings processes.

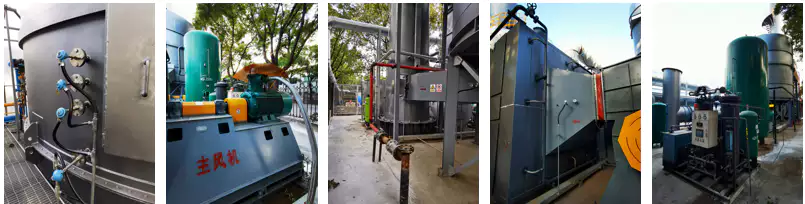
Pengenalan Syarikat
We are a high-tech enterprise specializing in the comprehensive treatment of volatile organic compounds (VOCs) waste gas and carbon reduction and energy-saving technology. Our core technologies include thermal energy, combustion, sealing, and self-control, with capabilities in temperature field simulation, air flow field simulation modeling, ceramic heat storage material performance, molecular sieve adsorption material selection, and VOCs organic matter high-temperature incineration oxidation characteristics testing.
Our team is comprised of over 360 employees, including more than 60 R&D technical elites. Our core technology team comes from the Aerospace Liquid Rocket Engine Research Institute (Aerospace Sixth Institute). We have an RTO technology research and development center and a waste gas carbon reduction engineering technology center in Xi’an, and a 30,000 square meter production base in Yangling. We are a leading manufacturer of RTO equipment and molecular sieve rotary equipment in the world.
Our core products include rotary valve-type heat storage oxidation incinerator (RTO) and molecular sieve adsorption concentration rotary wheel. Combining our expertise in environmental protection and thermal energy system engineering technology, we can provide customers with comprehensive solutions for industrial waste gas treatment and carbon reduction with various working conditions.
Pensijilan, Paten dan Kepujian
- Pensijilan Sistem Pengurusan Harta Pengetahuan
- Pensijilan Sistem Pengurusan Kualiti
- Pensijilan Sistem Pengurusan Alam Sekitar
- Kelayakan Perusahaan Industri Pembinaan
- Perusahaan berteknologi tinggi
- Patents: Rotary-type Heat Storage Oxidation Furnace Rotary Valve Patent, Rotary Heat Storage Incineration Equipment Patent, Disc Molecular Sieve Rotary Wheel Patent, etc.
How to Choose the Suitable RTO for Coating Industry
RTO untuk Industri Salutan” />
Choosing the appropriate RTO for coating industry requires careful considerations in the following aspects:
- Determine the characteristics of the exhaust gas
- Understand the local regulations and set emission standards
- Menilai kecekapan tenaga
- Pertimbangkan operasi dan penyelenggaraan
- Analisis belanjawan dan kos
- Choose the appropriate RTO type
- Pertimbangkan faktor persekitaran dan keselamatan
- Testing and verification of performance
Regenerative Thermal Oxidizers Service Process
Our service process for regenerative thermal oxidizers includes:
- Preliminary consultation, on-site inspection, and demand analysis
- Solution design, simulation, and solution review
- Customized production, quality control, and factory testing
- On-site installation, commissioning, and training services
- Regular maintenance, technical support, and spare parts supply
As a one-stop solution provider for RTO, our professional team can tailor RTO solutions for customers. We have successfully provided RTO solutions for the coating industry, including but not limited to the following cases:
- Shanghai-based company: the project is divided into two phases, with a 40,000 air volume RTO in the first phase and a 50,000 air volume RTO in the second phase.
- Guangdong-based new material technology company: the waste gas total amount is 70,000 m3/h, and the equipment meets the emission standards after completion.
- Zhuhai-based new material technology company: the main product is the wet lithium-ion battery separator, and the system has been running flawlessly since its self-operation.
Pengarang: Miya