Thermal oxidizers for paint booths
はじめに
Thermal oxidizers play a crucial role in the paint booth industry, providing an efficient and environmentally friendly solution for the treatment of volatile organic compounds (VOCs) emitted during painting processes. These advanced systems are designed to capture and destroy harmful pollutants, ensuring compliance with air quality regulations. In this article, we will explore the various aspects and benefits of thermal oxidizers for paint booths.
1. How do thermal oxidizers work?
– Thermal oxidizers utilize high temperatures to break down VOCs into carbon dioxide and water vapor through a process called oxidation.
– The VOC-laden air is drawn into the oxidizer chamber, where it is heated to the required temperature.
– The heated air then enters the combustion chamber, where a burner provides the necessary heat to maintain the desired temperature.
– As the VOCs pass through the combustion chamber, they react with oxygen and are converted into harmless byproducts.
– The purified air is then released into the atmosphere, meeting regulatory standards.
2. Types of thermal oxidizers
There are different types of thermal oxidizers available for paint booth applications, each with its own advantages and suitability for specific requirements:
2.1 Regenerative thermal oxidizers (RTOs)
– RTOs are highly efficient and widely used in the coating industry.
– They use a regenerative process that allows for the recovery of heat energy, reducing operating costs.
– The VOC-laden air passes through ceramic beds, where heat is transferred from the outlet air to the incoming air stream, preheating it.
– RTOs are known for their high destruction efficiency and can handle large volumes of exhaust air.
2.2 Catalytic oxidizers
– Catalytic oxidizers utilize catalysts to facilitate the oxidation reaction at lower temperatures.
– They are suitable for applications where low operating temperatures are required, thus saving energy.
– The catalysts promote the oxidation process, allowing for VOC destruction at lower temperatures than traditional thermal oxidizers.
– Catalytic oxidizers are often preferred for processes involving lower VOC concentrations.
2.3 Direct-fired thermal oxidizers
– Direct-fired thermal oxidizers burn the VOCs directly in the combustion chamber.
– They are well-suited for applications with high VOC concentrations and varying flow rates.
– Direct-fired oxidizers can handle a wide range of paint booth exhaust streams, providing flexibility in operation.
– These systems require careful monitoring to ensure complete combustion and prevent the formation of harmful byproducts.
3. Benefits of thermal oxidizers for paint booths
Thermal oxidizers offer several advantages for paint booth operators, such as:
3.1 Environmental compliance
– Thermal oxidizers effectively destroy VOCs, ensuring compliance with stringent air quality regulations.
– By eliminating harmful pollutants, these systems contribute to a cleaner and healthier environment.
3.2 Energy efficiency
– Certain types of thermal oxidizers, like RTOs, incorporate heat recovery mechanisms, reducing energy consumption and operating costs.
– The recovered heat can be used to preheat the incoming air, resulting in significant energy savings.
3.3 Process reliability
– Thermal oxidizers provide reliable and continuous VOC removal, allowing paint booth operations to run smoothly.
– These systems are designed to handle varying flow rates and maintain optimal performance even during peak production periods.
3.4 Improved air quality
– By eliminating VOC emissions, thermal oxidizers help improve indoor and outdoor air quality, creating a safer and healthier work environment.
結論
Thermal oxidizers have revolutionized the paint booth industry by offering an efficient and sustainable solution for VOC abatement. Their ability to effectively destroy harmful pollutants, coupled with energy-efficient operation, makes them an indispensable component for any paint booth facility. By investing in thermal oxidizers, businesses can ensure compliance with environmental regulations while prioritizing worker safety and well-being.

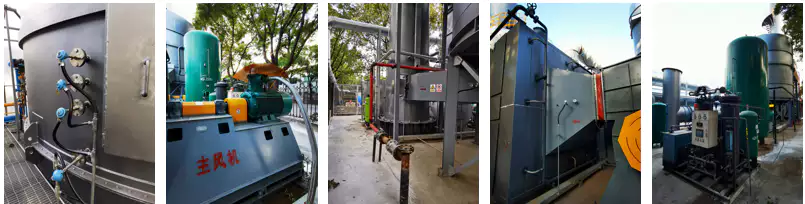
会社紹介
We are a high-tech equipment manufacturing enterprise that focuses on comprehensive treatment of volatile organic compound (VOCs) exhaust gases and carbon reduction and energy-saving technologies. Our core technologies include thermal energy, combustion, sealing, and self-control. We have the capabilities for temperature field simulation, air flow field simulation modeling, ceramic heat storage material performance, molecular sieve adsorbent material selection, and VOCs organic compound high-temperature incineration and oxidation experimental testing.
チームアドバンテージ
We have an RTO technology research and development center and waste gas carbon reduction engineering technology center in Xi’an, as well as a 30,000 square meter production base in Yangling. We are a leading manufacturer of RTO equipment and molecular sieve rotary equipment in terms of production and sales globally. Our core technical team comes from the Aerospace Liquid Rocket Engine Research Institute (Aerospace Six Institute). We currently have more than 360 employees, including over 60 research and development technology backbone, including 3 senior engineers, 6 senior engineers, and 26 thermodynamics doctors.
コア製品
Our core products include the Rotary Valve Thermal Oxidation Incinerator (RTO) and molecular sieve adsorption concentration wheel. Combined with our expertise in environmental protection and thermal energy system engineering, we can provide customers with comprehensive solutions for industrial exhaust gas treatment and carbon reduction with thermal energy utilization under various operating conditions.
認定、特許、栄誉
- 知的財産管理システム認証
- 品質管理システム認証
- 環境マネジメントシステム認証
- 建設業企業資格
- ハイテク企業
- Patent for Rotary Valve Thermal Oxidation Furnace
- Patent for Rotary Heat Storage Incineration Equipment
- Patent for Disc Molecular Sieve Wheel
Choosing the Right RTO for the Coating Industry
When selecting an RTO for the coating industry, it is important to:
- 排気ガスの特性を判断する
- 地域の規制と排出基準を理解する
- エネルギー効率を評価する
- 運用とメンテナンスを考慮する
- 予算とコストを分析する
- Select the appropriate type of RTO
- 環境と安全の要素を考慮する
- Perform performance testing and validation
Regenerative Thermal Oxidizers Service Process
Our service process for regenerative thermal oxidizers includes:
- Initial consultation, on-site inspection, and needs analysis
- ソリューション設計、シミュレーションモデリング、ソリューションレビュー
- Custom production, quality control, and factory testing
- オンサイト設置、試運転、トレーニングサービス
- 定期的なメンテナンス、技術サポート、スペアパーツの供給
We are a one-stop solution for RTOs and have a professional team that customizes RTO solutions for our customers.
RTO for Coating Industry Success Cases
- Case 1: A company in Shanghai specializes in functional films such as diffusion membrane, prism membrane, micro-porous membrane, and solar film. The project consists of a first phase with a 40,000 air volume RTO and a second phase with a 50,000 air volume RTO.
- Case 2: A company in Guangdong specializes in products such as transfer paper, transfer film, aluminum foil, polyester film, window film, and protective film. The total exhaust gas volume is 70,000 m3/h, and the equipment meets emission standards after construction.
- Case 27: A company in Zhuhai specializes in wet lithium battery separators, and the system has been running without any failures since its operation.
著者宮