Какви са най-новите постижения в RTO технологията за индустрията за покрития?
Introduction
The coating industry plays a crucial role in various sectors, including automotive, aerospace, and construction. As environmental regulations become more stringent, the demand for sustainable solutions in the coating process continues to rise. Regenerative Thermal Oxidizer (RTO) technology has emerged as a pioneering solution in mitigating emissions and enhancing energy efficiency. In this article, we will explore the latest advancements in RTO technology and their impact on the coating industry.
Advancement 1: Enhanced Heat Recovery Efficiency
– RTO systems have witnessed significant improvements in heat recovery efficiency. Through advancements in ceramic media design, the heat transfer capabilities have been optimized, resulting in better energy conservation during the oxidization process.
– This improved efficiency allows for a more sustainable coating industry by reducing the overall energy consumption and minimizing the carbon footprint.
– The image below illustrates a modern RTO system design, showcasing its compact and efficient configuration.

Advancement 2: Intelligent Process Control
– With the integration of advanced control systems and sensors, RTO technology now offers intelligent process control capabilities.
– Real-time monitoring of key parameters such as temperature, pressure, airflow, and VOC concentrations allows for precise adjustments, ensuring optimal performance and compliance with environmental regulations.
– The implementation of intelligent process control enhances the overall operational efficiency and reliability of RTO systems in the coating industry.
Advancement 3: VOC Destruction Efficiency
– Volatile Organic Compounds (VOCs) are a common byproduct of the coating process and pose environmental risks. The latest advancements in RTO technology have led to improved VOC destruction efficiency.
– RTO systems now offer higher destruction rates, often exceeding 99%, ensuring that harmful emissions are minimized.
– This advancement enables the coating industry to maintain regulatory compliance while reducing the environmental impact associated with VOC emissions.
Advancement 4: Flexibility and Adaptability
– Modern RTO systems are designed to be flexible and adaptable to the evolving needs of the coating industry.
– They can handle a wide range of coating applications, including solvent-based, water-based, and powder coatings.
– The ability to adapt to different coating processes and accommodate varying volumes of exhaust air makes RTO technology a versatile solution for the coating industry.
Заключение
In conclusion, the latest advancements in RTO technology have revolutionized the coating industry by offering enhanced heat recovery efficiency, intelligent process control, improved VOC destruction efficiency, and flexibility. These advancements contribute to a more sustainable and environmentally friendly coating process. As the industry continues to evolve, RTO technology will play a vital role in meeting regulatory requirements and reducing the environmental impact of the coating industry.
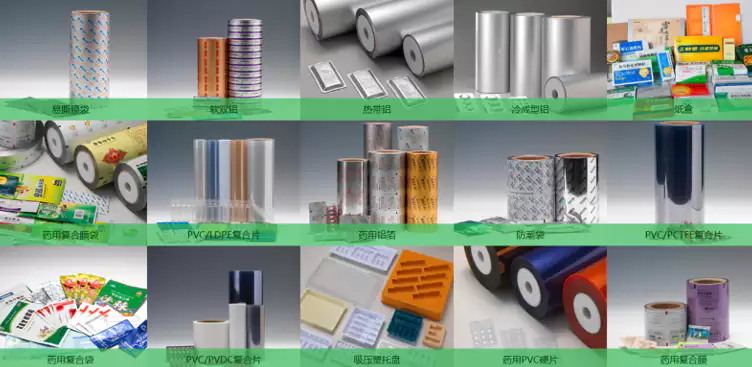
Latest Advancements in RTO Technology for the Coating Industry
Our company specializes in high-end equipment manufacturing for comprehensive treatment of volatile organic compounds (VOCs) and carbon reduction and energy-saving technologies. We have four core technologies: thermal energy, combustion, sealing, and self-control.
Our team has a RTO technology R&D center and a waste gas carbon reduction engineering technology center in Xi’an, and a 30,000©O production base in Yangling. We are a leading global manufacturer of RTO equipment and zeolite molecular sieve rotary equipment. Our core technology team comes from the Aerospace Liquid Rocket Engine Research Institute (Sixth Academy of Aerospace).
Our core products are RTO and zeolite molecular sieve adsorption and concentration rotary equipment. With our expertise in environmental protection and thermal energy system engineering technology, we can provide customers with comprehensive solutions for industrial waste gas treatment and carbon reduction and energy utilization under various working conditions.
Certifications, Patents, and Honors
Our company has obtained various certifications and qualifications, including the Intellectual Property Management System Certification, Quality Management System Certification, Environmental Management System Certification, Construction Enterprise Qualification, High-tech Enterprise Certification, RTO Rotary Valve Patent, Rotary Heat Storage Oxidation Furnace Patent, Disc-type Zeolite Rotary Patent, etc.
How to Choose the Right RTO for Coating Industry
- Determine waste gas characteristics
- Understand local regulations and emission standards
- Evaluate energy efficiency
- Consider operation and maintenance
- Budget and cost analysis
- Select the appropriate RTO type
- Consider environmental and safety factors
- Performance testing and verification
It is important to carefully evaluate each of these factors in order to choose the right RTO for the coating industry. This will ensure that your industrial waste gas treatment is efficient, cost-effective, and meets all necessary regulatory requirements.
RTO for Coating Industry“>
Regenerative Thermal Oxidizers Service Process
- Preliminary consultation, on-site inspection, and demand analysis
- Solution design, simulation modeling, and scheme review
- Customized production, quality control, and factory testing
- On-site installation, commissioning, and training services
- Regular maintenance, technical support, and spare parts supply
Our company provides a one-stop solution for RTO, with a professional team that can tailor RTO solutions to meet customer needs. We have successfully helped many customers in the coating industry with their waste gas treatment needs.
Successful RTO for Coating Industry Cases
- Project 1: A Shanghai-based enterprise specializing in functional films such as diffusion films, prism films, micro-permeable films, and solar films. The project is divided into two phases, with a 40,000 wind volume RTO in the first phase and a 50,000 wind volume RTO in the second phase.
- Project 2: Guangdong-based new material technology company specializing in transfer paper, transfer film, electrochemical aluminum, polyester film, window film, protection film, etc. The total amount of waste gas is 70,000 m3/h, and the equipment meets emission standards upon completion.
- Project 86: Zhuhai-based new material technology company specializing in wet lithium battery separators. The system has been running without fault since installation.
Автор: Мия