RTO performance in coating applications
Introduction
– Regenerative Thermal Oxidizers (RTOs) are crucial for ensuring optimum performance in coating applications. These highly efficient systems play a vital role in controlling volatile organic compounds (VOCs) emissions and maintaining air quality standards in the coating industry.
Advantages of RTOs
– Enhanced VOC destruction efficiency: RTOs use a regenerative process that enables them to achieve high destruction rates, typically above 99%. This ensures that VOC emissions from coating applications are significantly reduced, promoting environmental sustainability.
– Energy efficiency: RTOs are designed to recover and reuse heat energy, resulting in lower energy consumption and operating costs. By utilizing the heat generated during the oxidation process, RTOs contribute to the overall energy efficiency of coating operations.
– High reliability and durability: RTOs are built with robust materials and advanced engineering techniques, making them highly reliable and durable. This ensures that the system can withstand the demanding conditions of coating applications while maintaining consistent performance.
– Flexibility in handling varying process conditions: RTOs can adapt to different process conditions, including varying pollutant concentrations and flow rates. This flexibility allows for efficient VOC abatement across a wide range of coating applications, ensuring compliance with regulatory standards.
– Minimal maintenance requirements: RTOs are designed for ease of maintenance, with features such as automated controls and self-cleaning mechanisms. This minimizes downtime and reduces the need for frequent maintenance, enabling continuous operation and productivity in coating processes.
Key components of RTOs
– Heat exchangers: RTOs consist of multiple heat exchangers that facilitate the transfer of heat between the outgoing and incoming gas streams. The heat exchangers are responsible for the energy recovery process, maximizing the system’s efficiency.
– Ceramic beds: RTOs utilize ceramic beds as the regenerative media. These beds have a high thermal mass and can store and release heat efficiently during the cyclic operation of the system.
– Burner system: The burner system provides the necessary heat for the oxidation process. It is designed to ensure complete combustion of VOCs and maintain the required operating temperature for optimal performance.
– Control system: RTOs are equipped with advanced control systems that monitor and regulate various parameters, including temperature, flow rates, and pressure differentials. The control system ensures precise and reliable operation, contributing to the overall performance of the RTO.
Applications of RTOs in coating industry
– Automotive coating: RTOs are extensively used in automotive coating facilities to control VOC emissions and comply with strict environmental regulations. The high destruction efficiency of RTOs ensures that the volatile compounds released during the coating process are effectively treated, preventing air pollution.
– Industrial coating: RTOs play a crucial role in industrial coating applications, where large-scale operations generate significant amounts of VOCs. By implementing RTOs, industrial coating facilities can reduce their environmental footprint and maintain a safe and sustainable working environment.
– Furniture and woodworking coating: The furniture and woodworking industry often involves the use of coatings that contain VOCs. RTOs provide an efficient solution for mitigating the emissions from these processes, protecting both workers’ health and the environment.
– Aerospace coating: RTOs are employed in aerospace coating applications to eliminate VOCs and ensure compliance with stringent air quality regulations. The high reliability and adaptability of RTOs make them well-suited for the demanding requirements of the aerospace industry.
Заключение
– RTOs offer exceptional performance in coating applications, providing efficient VOC abatement and contributing to a sustainable and environmentally friendly coating industry. With their advantages in VOC destruction efficiency, energy efficiency, reliability, and flexibility, RTOs have become an integral part of coating operations across various sectors. The use of RTOs enables coating facilities to meet regulatory standards, minimize environmental impact, and enhance overall operational efficiency.

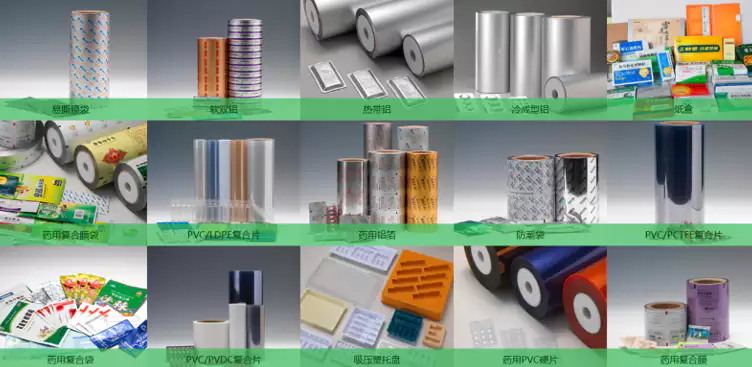
Introduction
We are a high-tech enterprise specializing in the comprehensive treatment of volatile organic compounds (VOCs) and carbon reduction and energy-saving technologies. Our core technologies include thermal energy, combustion, sealing, and self-control. We have the ability to simulate temperature fields and airflow fields, model calculations, compare ceramic heat storage material properties, molecular sieve adsorption materials, and VOCs. We have established an RTO technology research and development center and a waste gas carbon reduction engineering technology center in Xi’an, and a 30,000 square meter production base in Yangling. We are a leading manufacturer of RTO equipment and molecular sieve rotary equipment worldwide, with a team of over 360 employees, including more than 60 R&D technology backbones, three research fellows, six senior engineers, and 35 thermodynamics PhDs.
Certifications and Qualifications
Our company has obtained various certifications and qualifications including knowledge property management system certification, quality management system certification, environmental management system certification, construction industry enterprise qualifications, high-tech enterprise, rotary valve patent for rotary heat storage oxidation furnace, rotary heat storage incineration equipment patent, and molecular sieve rotary disc patent.
Choosing the Right RTO for Coating Industry
Choosing the right RTO for the coating industry involves determining waste gas characteristics, understanding local regulations and emission standards, evaluating energy efficiency, considering operation and maintenance, budget analysis, selecting the appropriate RTO type, environmental and safety considerations, and performance testing and verification.
Regenerative Thermal Oxidizers Service Process
Our service process includes initial consultation, site inspection, demand analysis, program design, simulation and simulation, program review, customized production, quality control, factory testing, on-site installation, commissioning and operation, training services, regular maintenance, technical support, and spare parts supply.
We are committed to providing one-stop RTO solutions with a professional team to customize RTO solutions for customers. We have successfully provided RTO solutions for coating industry including:
- Shanghai Company: Two phases of the project, with RTOs of 40,000 and 50,000 air volume respectively. The main products include diffusion films, prism films, micro-porous films, and sun films.
- Guangdong Company: The total amount of waste gas is 70,000 m3/h, and the equipment meets the emission standards.
- Zhuhai Company: The main product is the wet lithium battery diaphragm, and the system has been operating without failure since its self-operation.
Автор: Мия