How to ensure RTO compliance with local regulations in the coating industry?
Giới thiệu
The coating industry plays a crucial role in various sectors, including manufacturing, automotive, and aerospace. As environmental regulations become more stringent, it is essential for coating facilities to ensure compliance with local regulations. One effective way to achieve compliance is by implementing Regenerative Thermal Oxidizers (RTOs). In this article, we will explore the different aspects and angles of how to ensure RTO compliance with local regulations in the coating industry.
Understanding RTOs
– RTOs, or Regenerative Thermal Oxidizers, are air pollution control systems widely used in the coating industry.
– They work by using high temperatures to oxidize volatile organic compounds (VOCs) and hazardous air pollutants (HAPs) emitted during coating processes.
– RTOs employ a regenerative process that allows for high energy efficiency and lower operating costs.
Local Regulations and Compliance
– Each region and country has specific regulations governing air pollution and emissions from industrial processes, including coating facilities.
– It is vital for coating industry operators to thoroughly understand and comply with these local regulations to avoid penalties and maintain a sustainable operation.
– RTOs provide an effective solution for meeting the emissions standards set by local authorities.
Factors Influencing RTO Compliance
1. Technical Specifications:
– RTOs must be designed and sized appropriately to handle the specific exhaust volume and composition of VOCs and HAPs generated by the coating process.
– The engineering design should consider factors such as temperature requirements, airflows, and residence time to ensure efficient destruction of pollutants.
2. Monitoring and Control:
– Coating facilities must implement robust monitoring and control systems to continuously track emissions and ensure compliance with local regulations.
– Advanced sensors and data acquisition systems can provide real-time information on pollutant levels and allow for immediate corrective actions if necessary.
3. Maintenance and Inspections:
– Regular maintenance and inspections are crucial for RTOs to operate optimally and comply with local regulations.
– Routine inspections should include checks on combustion chambers, heat exchangers, valves, and other components to identify any potential issues that may affect compliance.
4. Training and Awareness:
– Proper training and awareness programs should be implemented for coating facility operators and maintenance personnel.
– This ensures that they understand the importance of compliance, know how to operate and maintain the RTO system correctly, and can troubleshoot any potential problems.
Phần kết luận
Ensuring RTO compliance with local regulations in the coating industry is of utmost importance for sustainable and environmentally responsible operations. By understanding the technical aspects, adhering to monitoring and control practices, conducting regular maintenance, and fostering training and awareness, coating facilities can achieve compliance and contribute to a cleaner environment. Implementing RTOs as an integral part of the coating process helps mitigate air pollution while maintaining operational efficiency and cost-effectiveness.

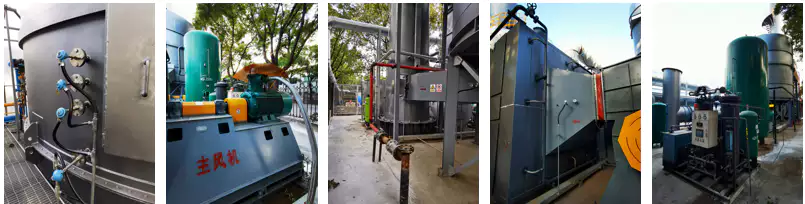
Ensuring RTO Compliance with Local Regulations in the Coating Industry
Our company is a high-tech enterprise that specializes in the comprehensive management of volatile organic compounds (VOCs) and carbon reduction energy-saving technology. With core technologies in thermal energy, combustion, sealing, and automatic control, we have the ability to simulate temperature and airflow fields, as well as test and evaluate the performance of ceramic heat storage materials, zeolite molecular sieve adsorption materials, and high-temperature incineration and oxidation of VOCs.
With a team of more than 360 employees, including over 60 R&D technology experts, we have established RTO technology research and development centers and waste gas carbon reduction engineering technology centers in Xi’an, and have a 30,000 square meter production base in Yangling. Our core technology team comes from the Aerospace Liquid Rocket Engine Research Institute (Aerospace Sixth Institute). We are the world’s leading manufacturer of RTO equipment and zeolite molecular sieve rotary equipment, providing customers with comprehensive solutions for industrial waste gas treatment and carbon reduction through our environmental and thermal energy system engineering technology expertise.
Chứng nhận, Bằng sáng chế và Danh hiệu
Our company has received various certifications and qualifications, including knowledge property management system certification, quality management system certification, environmental management system certification, construction industry enterprise qualification, high-tech enterprise certification, and patents for RTO rotary valve, rotary heat storage incineration equipment, and plate zeolite rotary equipment, among others. Our company has also been recognized with numerous honors, such as the National Innovation Award, Science and Technology Progress Award, and Environmental Protection Contribution Award.
Choosing the Right RTO for the Coating Industry
When choosing the right RTO for the coating industry, it is important to consider several factors:
- Xác định đặc tính của khí thải
- Hiểu các quy định và tiêu chuẩn khí thải của địa phương
- Đánh giá hiệu quả năng lượng
- Xem xét hoạt động và bảo trì
- Conduct budget and cost analysis
- Choose the appropriate RTO type
- Consider environmental and safety concerns
- Conduct performance testing and verification
Each of these factors plays a crucial role in ensuring compliance with local regulations and optimizing the overall performance of the RTO system. Our team of experts can guide our customers throughout the selection process to ensure the most appropriate RTO system is selected.
Regenerative Thermal Oxidizers Service Process
Our company’s RTO service process includes:
- Initial consultation, site inspection, and needs analysis
- Proposal design, simulation, and proposal review
- Custom production, quality control, and factory testing
- On-site installation, commissioning, and training services
- Regular maintenance, technical support, and spare parts supply
Our one-stop RTO solution provides customers with a tailor-made RTO solution designed by our professional team. With the most advanced technology and equipment, our RTO system provides high-quality and efficient waste gas treatment and carbon reduction for the coating industry.
Here are some successful RTO cases for the coating industry:
- Project for a Shanghai-based enterprise that specializes in functional films with a 40,000 air volume RTO for the first phase and a 50,000 air volume RTO for the second phase
- Project for a Guangdong-based new material technology company with a total waste gas volume of 70,000 m3/h. After installation, the equipment meets emission standards
- Project for a Zhuhai-based new material technology company that specializes in wet lithium battery separators, with a system that has been running flawlessly since its installation
Tác giả: Miya